3D scanners have rapidly gained popularity within several industries as a go-to tool for creating high-accuracy measurements and high-quality digital twins for designing. Each industry has unique challenges and pain points that 3D scanners can help address.
With several types of scanners and methods of capturing data, users can find a use for this technology to provide reassurance and insight into design and inspection factors that may have been impossible before.
One industry that has particularly benefited from implementing scanners is industrial manufacturing and repair.
In this blog, we’ll explore why 3D scanners have become widely used within the industrial manufacturing space, the types of scanners used in this industry, and examples of the technology used to solve real-world problems.
Where Do Scanners Fit into Industrial Manufacturing?
Whenever there is a need to speed up project timelines or reduce costs by minimizing material waste, a solution will be sought.
For industrial manufacturing, this need is ever-present, especially due to the size of the items made and used.
How They Change the Game in Manufacturing Operations
The time to take measurements, training operators to use specialized equipment, and approval processes of data are pain points that can slow down a project dramatically or create wasted material by not having fitted items, requiring post-processing to correct.
For manufacturers looking to create retrofits on equipment, install new devices in a warehouse, or inspect wear over time on a machine, these tasks can be tedious to measure by hand due to their size.
They may require specialized tools, involve going into dangerous places for measurements, and can introduce human errors that must be checked several times. By using 3D scanners, a single operator can cover several feet of equipment or space in minutes without ever having to be close to the space.
Additionally, scanners are designed to have a simple user experience, so operators can be trained quickly on the device and make accurate scans, with many skills carrying over to different scanner technology.
With data captured by a calibrated and certified device, you can feel confident that the data has a high level of accuracy to the real-world object, reducing the amount of approval needed before using the data for design and inspection.
Many scanners display the data during the scanning process, allowing users to quickly identify and correct errors before moving on.
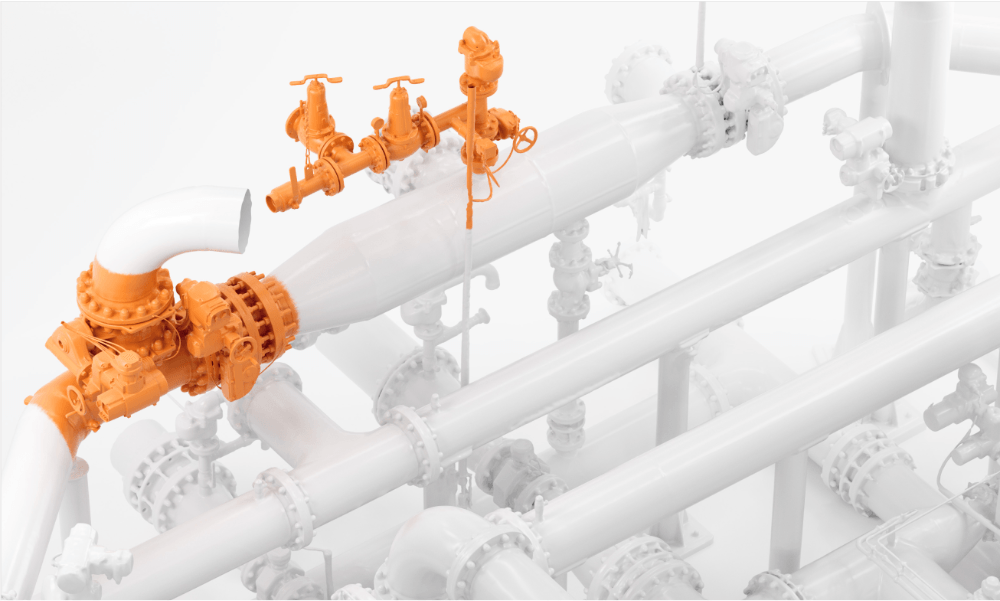
Which 3D Scanners Are Used in Industrial Manufacturing & Inspection?
If you’ve researched 3D scanners, you may have come across terms like handheld, desktop, and LiDAR. How do you know which is the right device for you?
These terms indicate how the device is held and captures data, and depending on the individual project, one may benefit over the other.
For industrial manufacturing, two types stand out as industry standards due to their capturable object size and data quality: Handheld and LiDAR.
1. LiDAR Scanners
LiDAR scanners, like the Artec Ray II, are long-range laser scanners that are typically mounted onto a tripod to remain stationary during the scanning process. They capture points in evenly spaced distances, resulting in cleaner surface details when processing the larger data set.
Their key benefits include:
- Far Scanning Range: Most LiDAR scanners can scan 100 meters or more and have variable levels of resolution to help see small features at that distance.
- 360-Degree Scanning View: The scanner rotates along a horizontal axis while the laser spins vertically, capturing all surfaces within the line of sight of the scanner.
- High Levels of Accuracy: The speed of the device, sensors, and mounted cameras for positioning give LiDAR scanners a high level of accuracy of the current state of the object and can be aligned with other scans to create a complete image of the item of interest.
2. Handheld Scanners
Handheld scanners, like the Artec Leo, are compact in size, allowing the operator to hold them in their hands. They capture the object while being moved around, giving you multiple angles to be scanned without repositioning the object.
Their key benefits include:
- Easy to Maneuver: Due to the lighter weight and portability, a wrist movement can capture several angles that may have required repositioning a stationary device multiple times to achieve.
- Compact Size: A smaller scanner allows users to scan in smaller places or reach into areas humans can’t enter to capture critical information for designing.
- Travel Friendly: Many handheld scanners fit within a small case and can be set up in remote locations, controlled environments, or on-site. They can also be recalibrated at these locations for increased accuracy.
The Best of Both Worlds: Using LiDAR & Handheld Scanners Together
LiDAR scanners are used to capture several meters of space by moving the device to multiple locations to create a large 3D dataset representing the space with a high level of accuracy.
Handheld scanners can then capture critical locations, complex features, or individual components with higher resolution.
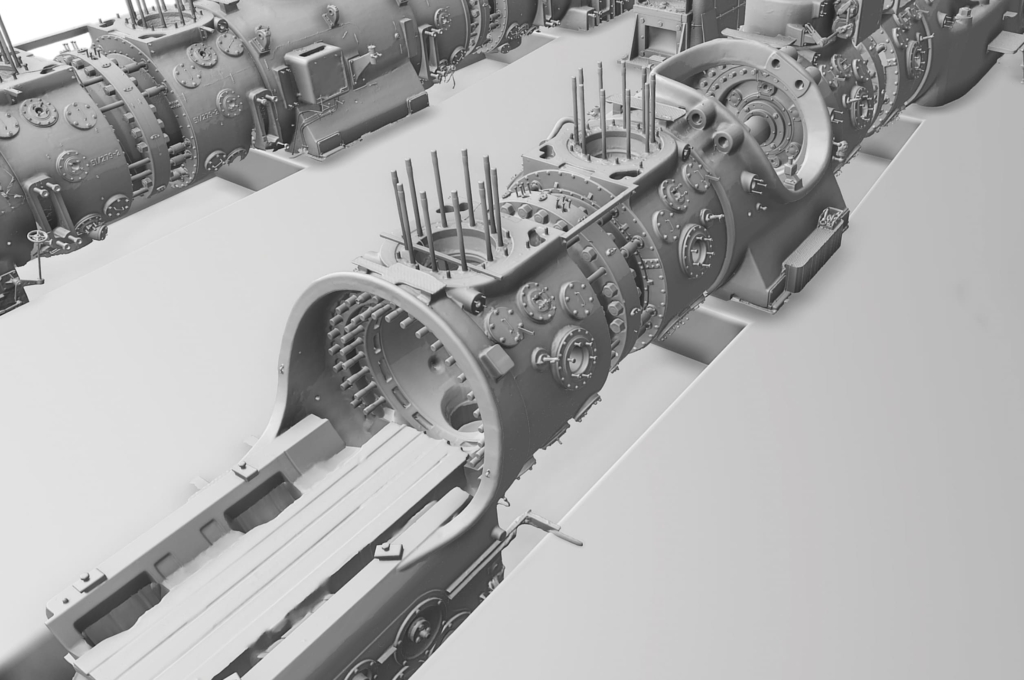
By aligning the two datasets, you can have the best of both worlds: high levels of accuracy from the LiDAR scanner and high resolution on features with the handheld scanner.
How Scan Data Is Used for Industrial Manufacturing
The end product of scanners is point-clouds/mesh data representing the real-world object in a digital space.
As a digital file, you can implement it in several CAD and inspection tools to remove the guesswork for design and provide insight into subtle features for inspection.
There are four ways this data can be used for industrial manufacturing.
1. Site Inspection
A single LiDAR scanner can capture entire sites in minutes instead of hours by multiple people. The 3D mesh created from the scanner can be used to find distances between objects, identify changes over time at the site, or create detailed reference geometry to design around.
2. Reverse Engineering Legacy Components
3D scanners can digitize older components that need replacement and have no original CAD files. By bringing the data into reverse engineering software, new surfaces, sketches, and references can be extracted and used to remake and redesign the part.
3. Feature Mapping and Reference Feature Extraction
Whether high up on the roof of a building, along an expanse of wall, or inside a machine, 3D scanners can identify how wires or pipes have been laid out and make measurements to verify angularity and distances between bends.
If you are planning a new layout, the same scanner can digitize the space and create reference points for designers.
4. Inspecting Equipment and Parts
With millions of points captured and small features visible with scan data, it’s easy to create high-quality inspection reports and find defects on equipment that would be difficult to find with hand measurements only.
Scanning often speeds up inspection routines, allowing for additional parts to be measured in the same amount of time it would take to measure a single part by hand.
The high levels of detail captured also allow users to make informed decisions on where to make repairs and manufacturing changes.
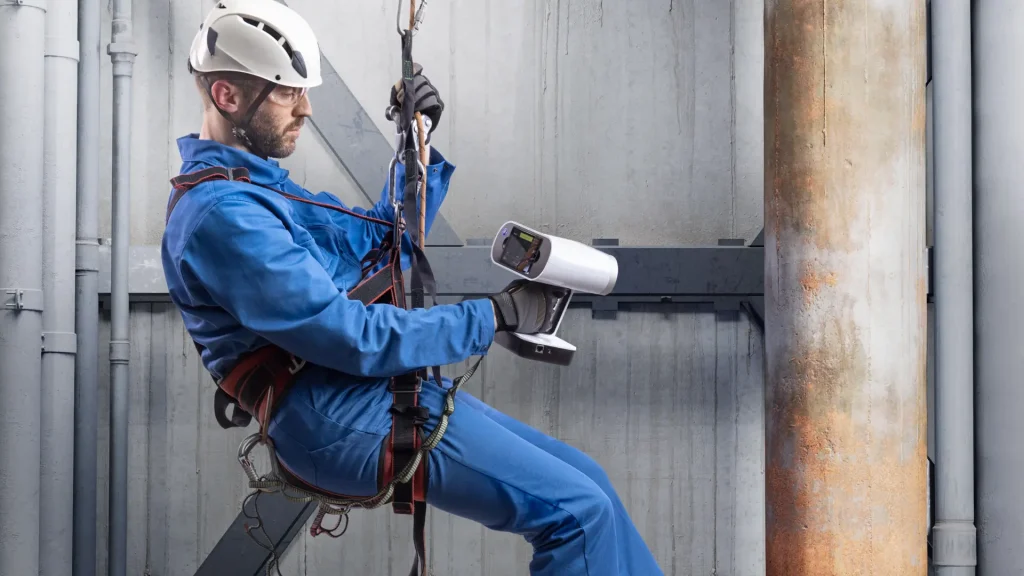
The Final Note
By reducing measurement times, providing reassurance that the data captured is accurate for inspections, and digitizing complex components for informed design decisions, the return on investment for a 3D scanner for industrial manufacturing is quick to see.
With different types of scanners ranging in capturable size and methods of creating data points, there isn’t a situation where a 3D scanner cannot be used to help capture spaces or objects for industrial applications.
If you are interested in learning more about the different types of scanners and how they can be used for your project, contact us today!