3D printing is known as one of the most sustainable manufacturing methods. It’s an additive process unlike traditional methods like milling or turning, which are subtractive.
In subtractive manufacturing, material is removed from a larger block until only the part remains, which produces a significant amount of waste.
In additive manufacturing, the part is built one layer at a time only using the material needed, so much less waste is produced.
Still, even though 3D printing waste is only a fraction of the overall 18,500 tons of plastic waste produced every year in the U.S., it’s still estimated that around 5,000 tons of waste per year comes from additive manufacturing. It’s usually after they are used and discarded, so it does add up to significant waste in our landfills.
With the 3D printing industry estimated to triple in the next five to 10 years, it’s more important now than ever to start putting processes in place to recycle wasted material and used parts. Plus, recycling and reusing these materials could lead to significant savings for companies as their 3D printing volume increases over time.
In this blog, we will explore some of the latest methods for recycling filament in additive manufacturing.

Working with Recycling Companies
One major part of recycling filament is recycling the plastic spools that the filament comes on.
Anyone who has done a significant amount of printing probably has a stash of spools that they fantasize about recycling or making storage containers out of, but ultimately, wind up tossing them in a dumpster because they don’t have the time or know where to send them.
Over the years, we’ve had many Hawk Ridge Systems customers suggest filament manufacturers should have a recycling program where customers could send back the spools for reuse or recycling, but shipping spools around the world isn’t a very sustainable solution either.
1. Figure Out If the Material Is Recyclable
Probably one of the best things you can do is contact the manufacturer and find out what material their spools are made of, and then contact your favorite local waste disposal service that handles recycling.
For example, our partner Markforged manufactures spools that are made of polycarbonate, which is generally recyclable. Although Markforged doesn’t have a program to take back spools, they can be recycled locally, which is more sustainable anyway.
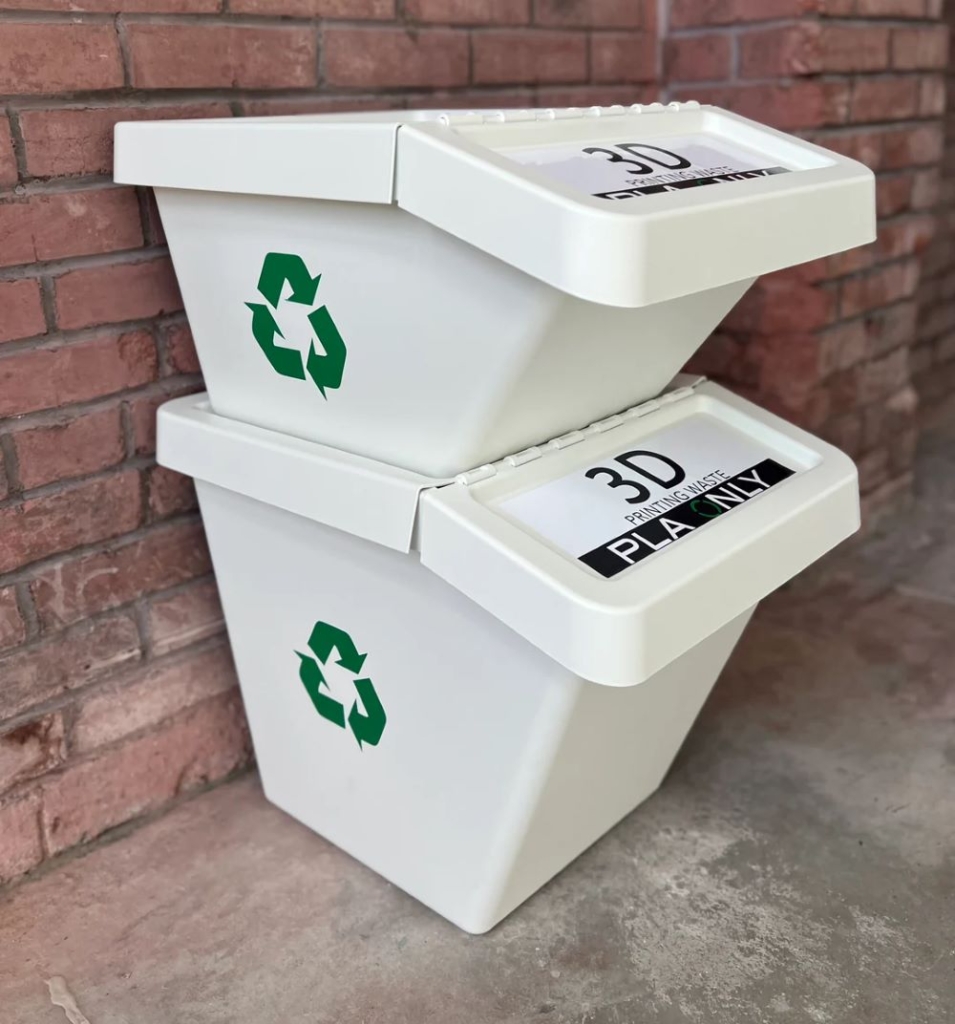
2. Find a 3D Printed Filament Recycler
Recycling 3D printing filament like PLA and ABS can be a little trickier as most are labeled as Class 7 and are not typically recyclable by municipal programs.
However, there are a lot of companies popping up that have recycling programs specifically for 3D printed filament. With a quick search online, I easily found Terracycle, FormFutura, and more.
Typically the way this works is:
- You label your waste material.
- Ship it to the recycler.
- Earn points for purchasing recycled filament.
So not only are you getting rid of your waste, but you’re also getting recycled material back to print with, which is even more sustainable and economical.
3 Steps to Recycling Filaments Yourself
The most sustainable method for recycling filament is going to be doing it yourself at the point of need.
If you want to recycle used filament and old parts, three pieces of equipment are necessary: a shredder, extruder, and spooler.
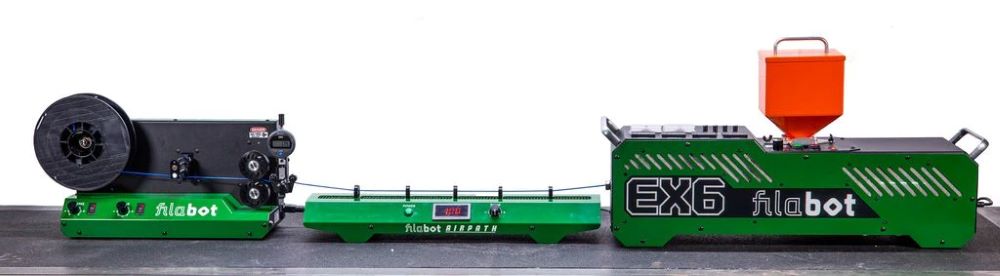
Step 1: Shred & Dry Your Material
First, the material must be shredded and broken into small pieces. If you are working with hygroscopic material that absorbs moisture, then you will need to dry your material before putting it into your extruder.
There are several solutions for drying shredded filament, including desiccant dryers, food hydrators, vacuum drying, and even oven drying is possible for the DIY’ers out there.
Desiccant dryers use a drying media like silica gel to give the moisture a more attractive target than your material. Typically, heat is used to free the moisture and then the desiccant traps it.
Food hydrators can be re-tasked for drying material if you’re looking for a more economical solution. Hot air passes over or through the material pulling the moisture out.
Using a vacuum dryer, air is removed, which increases pressure, lowering the moistures boiling point. This allows the material to be dried at a lower temperature without adding heat, which can be desirable depending on how sensitive it is to heat damage.
Oven drying is another option but is more hands-on and could lead to uneven drying potentially. The material is placed on a cookie sheet and slowly heated until the moisture is removed.
Markforged Onyx is an example of a hygroscopic material that would need drying. Felfil appears to have had success drying and recycling Onyx.
Step 2: Extrude the Plastic Pieces
The next step after shredding and drying is extruding, which turns the plastic pieces back into a cylindrical filament.
This is a crucial step as having a consistent filament diameter will affect print quality. After the material is formed back into a cylindrical shape, the next step is cooling it which typically happens using air or water cooling.
Step 3: Spool the Material for Use
Finally, a spooling machine is used to evenly spool your extruded material and prepare it for use. The material passes through rollers and is wound onto a spool and is ready for use.
Typically, spooling machines include filament diameter sensors, because if it’s off it could lead to poor extrusion and print quality.
Getting the Full Recycling Solution for Your Factory Floor
There are several companies that offer a full solution for recycling 3D printed filament, including all three pieces of equipment. The cost of these complete systems range from thousands to tens of thousands, which will exclude most hobbyist printers out there.
However for prosumer or industrial customers, it’s fairly reasonable compared to other equipment they are purchasing like CNC mills, lathes, press brakes, or even high-end 3D printers.
Plus, recycling filament saves money, so eventually over time these systems will pay for themselves as a return on investment is achieved.
Look at Ford, for example; it is currently saving money by recycling used printing powder from its HP multi jet fusion (MJF) system. The used powder is converted into pellets for injection molding, which is used to make clips for the fuel lines on the F-250.
HP does impressive work in reducing waste and finding ways to repurpose material. It’s just the beginning of this journey.
I believe Ellen Jackowski, who is the chief sustainability and social impact officer at HP, said it right about their collaboration with Ford’s sustainability efforts:
“You get more sustainable manufacturing processes with 3D, but we are always striving to do more, driving our industry forward to find new ways to reduce, reuse, and recycle powders and parts.”
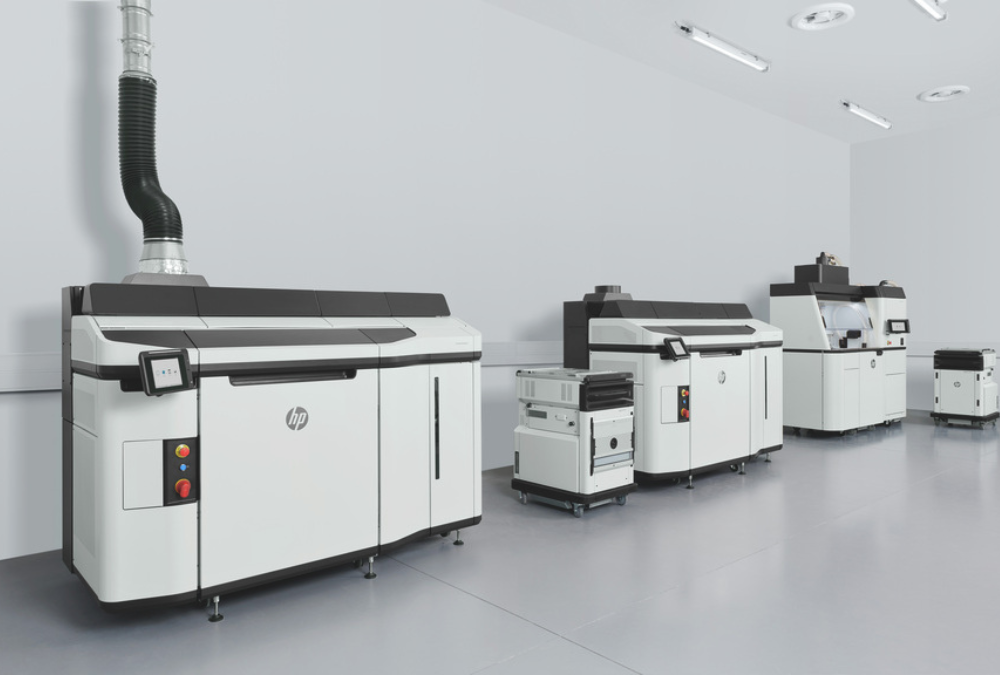
The Final Note
Hawk Ridge Systems offers everything you need to digitally manufacture parts from 3D scanners and CAD software to make models, 3D printers to produce them, and post-processing equipment to finish them.
If you would like to learn more or have questions, speak with one of our experts today!