HP Jet Fusion 5000 Series 3D Printers
Get Pricing Sent to You Today
While you are waiting, check out our Resource Center or read our Blog!
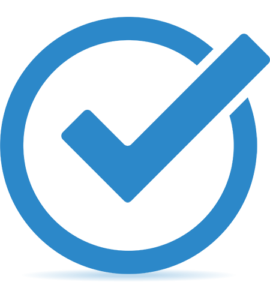
Reinvent How You Produce Prototypes and Functional Parts
HP Multi Jet Fusion 3D Printing Solutions, comprising the 5000, 5200, 5400, and 5600 models, represents industrial 3D printing systems designed for high-volume, high-quality production printing. Using a powder-based system, these printers lay down layers of still-molten material, ensuring complete fusion for fine details and repeatable, accurate, and strong parts consistently.
Among them, the 5200 series stands out for its remarkable speed and productivity, rivaling injection molding for short-run production, making it unmatched in the additive manufacturing world.
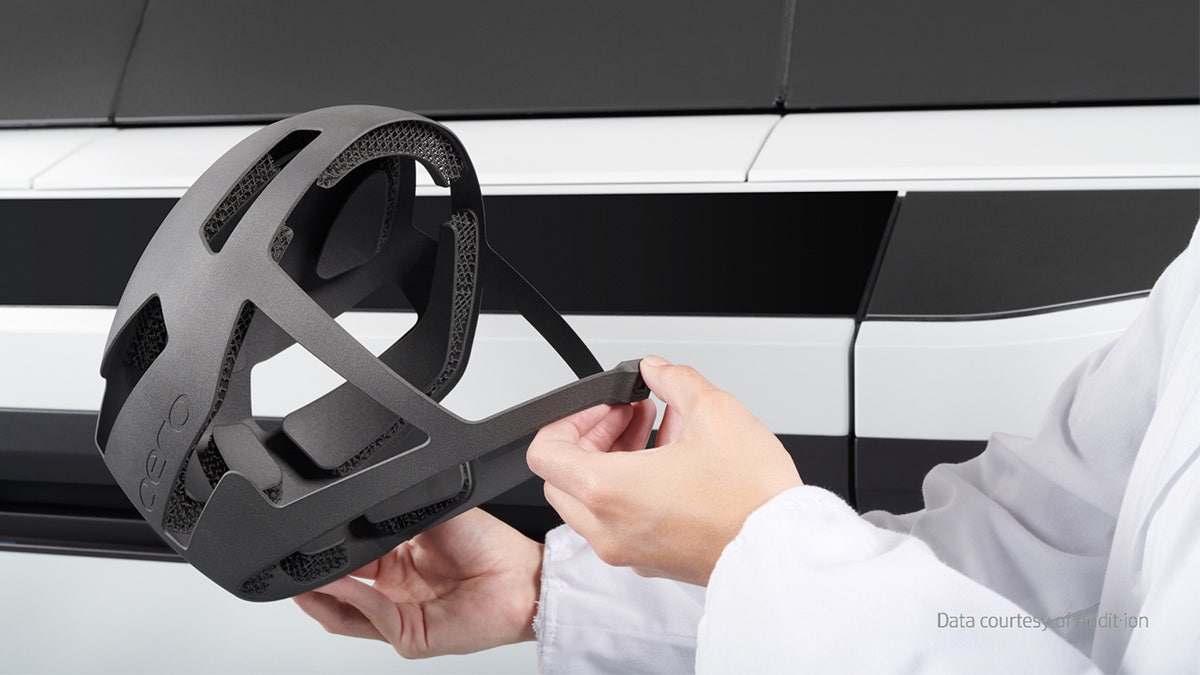
-
Material: PA12W
This robust thermoplastic provides the best balance between performance and reusability, for white functional parts across a variety of applications like prosthetics, medical equipment, lighting décor, fashion and wearables, and household appliances.
-
Material: PA12
Strong functional nylon material able to achieve highly detailed prints for end-use applications. PA12 is one of the least expensive materials from HP and is the most widely used material on an HP.
-
Material: PA11
Strong functional nylon material that has a high-quality surface finish with more flexibility compared to PA12.
-
Material: PA12GB
Glass-filled nylon material ideal for applications which require high stiffness and dimensional stability.
-
Material: TPU
Rubber-like, elastomeric material ideal for flexible applications.
-
Material: Polypropylene (PP)Low-cost material excellent for its chemical resistance, weldability, and low moisture absorption. This material is ideal for fluid movement applications.
-
Nesting & Build Prep Software
HP systems come with a free nesting and build prep software called Smart Stream Build Manager. This software works great for customers running lower quantities of parts. For high quantity production environments, it is recommended to use a 3rd party software such as Materialise Magics.
-
Fast Cooling 10.5 Hours
HP machines provide the option for natural or fast cooling. Natural cooling is recommended for parts that are long and thin, while fast cooling can be used in many cases to reduce the overall time to part in hand.
-
Natural Cooling Units (Optional Add-On)
Natural cooling units free up the post-processing stations and build units when printing multiple jobs in a row. Jobs can cool on the side while the user de-powders parts from a previous job in the post processing station. These are a less expensive alternative to purchasing additional build units.
-
Process Development PackageThe package includes software compatible with the 5600 printer, allowing for more control of the print process and parameters. Create your own print profiles and recipes. Then, dial in a print recipe for specific production runs of parts to optimize efficiency, part quality and part cost.
-
Processing StationThe Processing Station is used to unpack builds, load builds with powder and automatically recover and mix recycled powder. This closed- loop system reduces the amount of loose powder and mess associated with powdered fusion Printing.
-
Automation AccessoryThis system will automatically load a second build unit into the printer, allowing users to complete two consecutive prints without the need for human interaction once the first job has been started. Users experience much higher efficiency since this system can start the second job during off-hours like nighttime or weekends.
-
Automatic Unpacking StationThe Automatic Unpacking Station automatically unpacks builds and recovers recyclable powder for future use. This system saves approximately 30 minutes of human labor per job. It’s a great tool for those running high numbers of builds per week.
-
Powder Handling AutomationThis system enables higher productivity, better material quality and consistency and higher traceability between lots. The 3D Powder Handling Automation system is best for those running at least four printers and can handle up to 20 MJF 3D printers, eliminating the need for dedicated post- processing stations
Technical Specifications
Features
|
5000
|
5200
|
5420W
|
5600
|
---|---|---|---|---|
Print Speed
|
Up to 4010 cm3/hr
|
Up to 5058 cm3/hr
|
Up to 3380.84 cm3/hr
|
Up to 5058 cm3/hr
|
Build Volume
|
380mm (15”) x 284mm (11.2”) x 250mm (9.8”)
|
380mm (15”) x 284mm (11.2”) x 250mm (9.8”)
|
380mm (15”) x 284mm (11.2”) x 380mm (15")
|
380mm (15”) x 284mm (11.2”) x 380mm (15”)
|
Baseline Accuracy
|
±0.25mm (XY) ±0.42 (Z)
|
±0.25mm (XY) ±0.42 (Z)
|
±0.20mm (XY) ±0.42mm (Z)
|
±0.20mm (XY) ±0.42mm (Z)
|
Layer Thickness
|
80μm
|
80μm, 110μm
|
90μm
|
80-120 μm
|
Overall Printer Dimensions
|
2210mm (87”) x 1268mm (50”) x 1804mm (71”)
|
2210mm (87”) x 1268mm (50”) x 1804mm (71”)
|
2210mm (87”) x 1268mm (50”) x 1804mm (71”)
|
2210mm (87”) x 1268mm (50”) x 1804mm (71”)
|
Printer Operating Area
|
3700mm (146”) x 3700mm (146”) x 2500mm (99”)
|
3700mm (146”) x 3700mm (146”) x 2500mm (99”)
|
4100mm (161”) x 3700mm (146”) x 2500mm (99”)
|
3700mm (146”) x 3700mm (146”) x 2500mm (99”)
|
Printer Weight
|
880kg (1940lb)
|
880kg (1940lb)
|
880kg (1940lb)
|
880kg (1940lb)
|
Power Requirements
|
200-240V 3-Phase; 80A
|
200-240V 3-Phase; 80A
|
200-240V 3-Phase; 80A
|
200-240V 3-Phase; 80A
|
Fail Fast, Learn Faster
In the heart of the engineering building at San Jose State University, you’ll encounter a dedicated group of students passionately exploring various projects, from crafting jigs to optimizing batteries – they’re the Spartan Racing Electric team.
This self-driven squad tirelessly collaborates year-round, leveraging HP 3D printers to bring their innovative ideas to life for the prestigious Formula SAE Electric Competition.
Services & Customer Benefits
Technical Support
Unmatched Training
Professional Services
Frequently Asked Questions
Yes, there are different versions of each machine. These offer less expensive operating costs through material and consumable price breaks in exchange for a slightly higher hardware cost. For example, the 5200 has three variants: 5200, 5210, and 5210 PRO. The 5210 and 5210PRO will have cheaper individual part costs through discounts on raw powder and agents. The 5210 PRO offers bulk material ordering, significantly reducing the powder per kilogram cost.
- PA 12 thermoplastic for strong, low-cost parts
- PA 11 thermoplastic for ductile, impact-resistant parts
- PA 12 GB for stiff, dimensionally stable parts
- TPU and TPA for flexible, functional parts
- PP for chemical resistant, weldable parts
Ventilation and facility exhaust is optional, though it is recommended to improve the comfort level of the print room as well as reduce the overall heat dissipation in the room.
The post-processing station has multiple functions including:
- Loading and automatically mixing recycled powders with fresh material
- Unloading printed builds for initial de-powdering and cleaning of parts
- Cooling the build using fast cooling for expedited part retrieval
HP machines come with free nesting software called Smart Stream Build Manager. This software is sufficient to send jobs to the machine for print. It is very common for customers to purchase a 3rd party nesting software, such as Materialise Magics, for a much higher degree of nesting capability. Those focused on production typically opt for this 3rd party solution. Those focused on smaller volumes of prototypes typically stick with the free HP software.
Since HP Jet Fusion is a powder-based printing system, no support structure is generated; the powder is self-supporting. However, it is necessary to remove excess powder from the part exterior and interior through post-processing. This is commonly done by bead blasting parts.
Dimensional accuracy can vary depending on the material and printer. Here are some dimensional accuracy specification examples:
- A part 80mm in length printed out of PA 12 on the HP 5200: XY±.28mm ; Z±0.47mm.
- With Process Control Software, the 5200’s accuracy can improve to: XY±0.18 ; Z±0.30 for a part < 80mm.
- A part 80mm in length printed out of PA 12 on the HP 4200: XY±.31mm ; Z±1.12mm.
There are no performance differences between the 5200 series of printers. The differences between each model are cheaper consumables and materials with the 5210PRO providing the lowest part cost. The 5210PRO, for instance, can accept much larger material containers which significantly reduces the price per kg of material.
HP Jet Fusion Resources
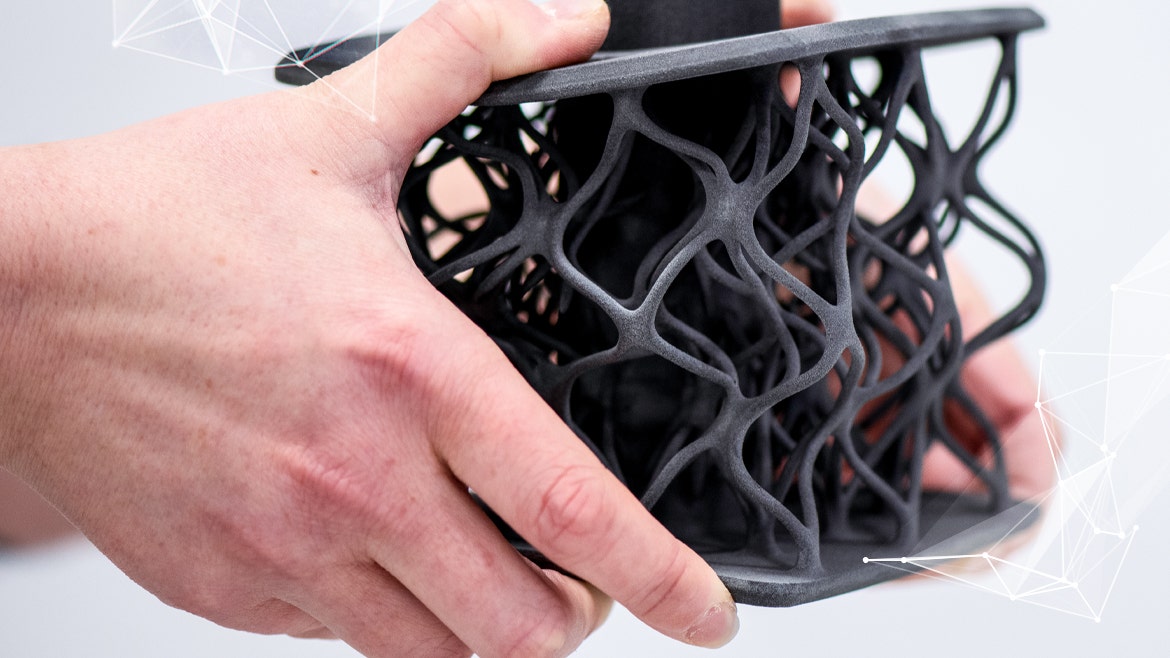
How Do HP Multi Jet Fusion 3D Printers Work?
Watch Video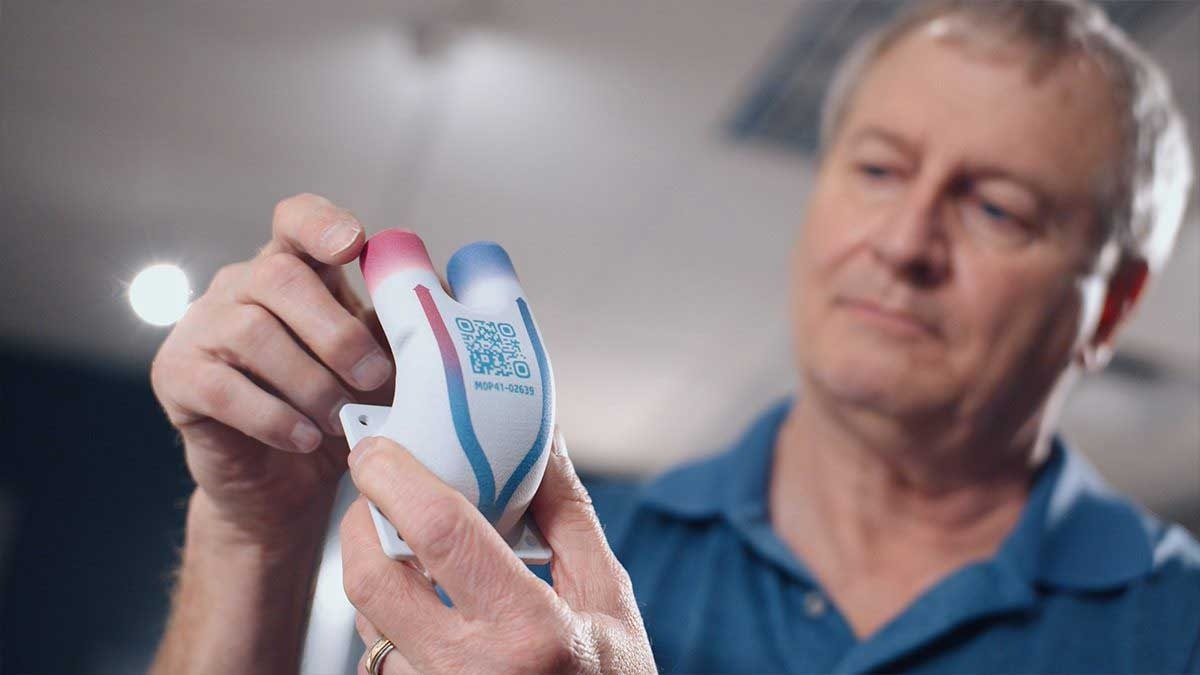
Diving Into Design for Additive Manufacturing
Watch Webinar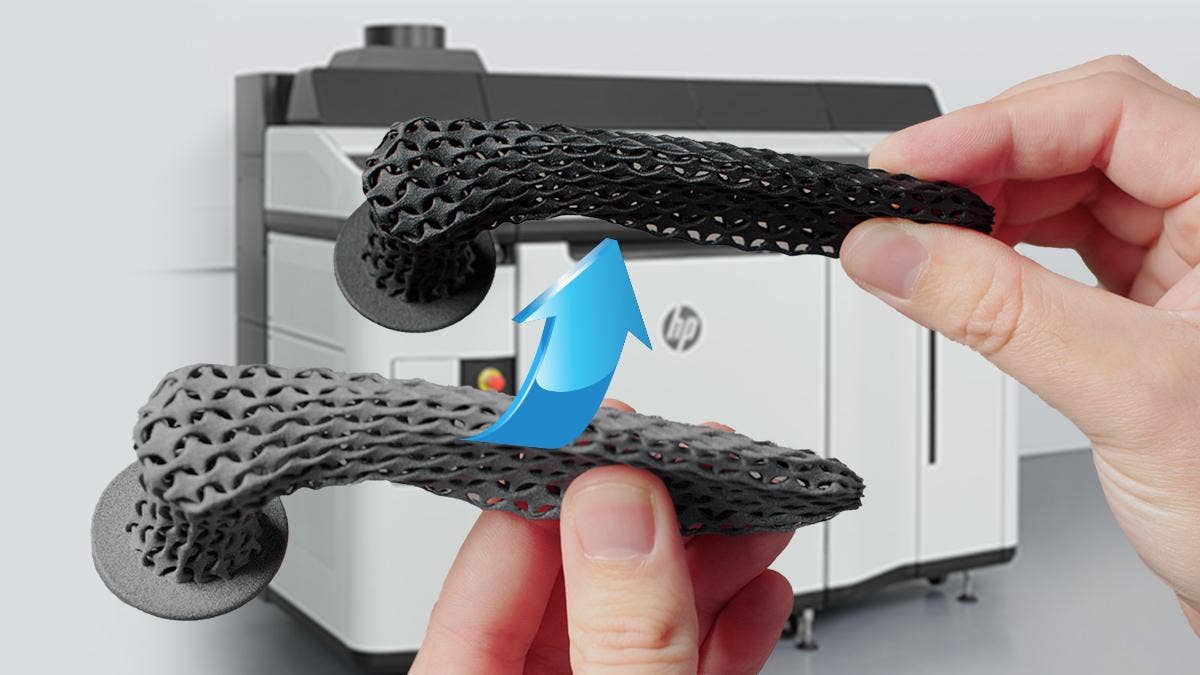
HP 3D Printing: What You Need To Know
Watch Video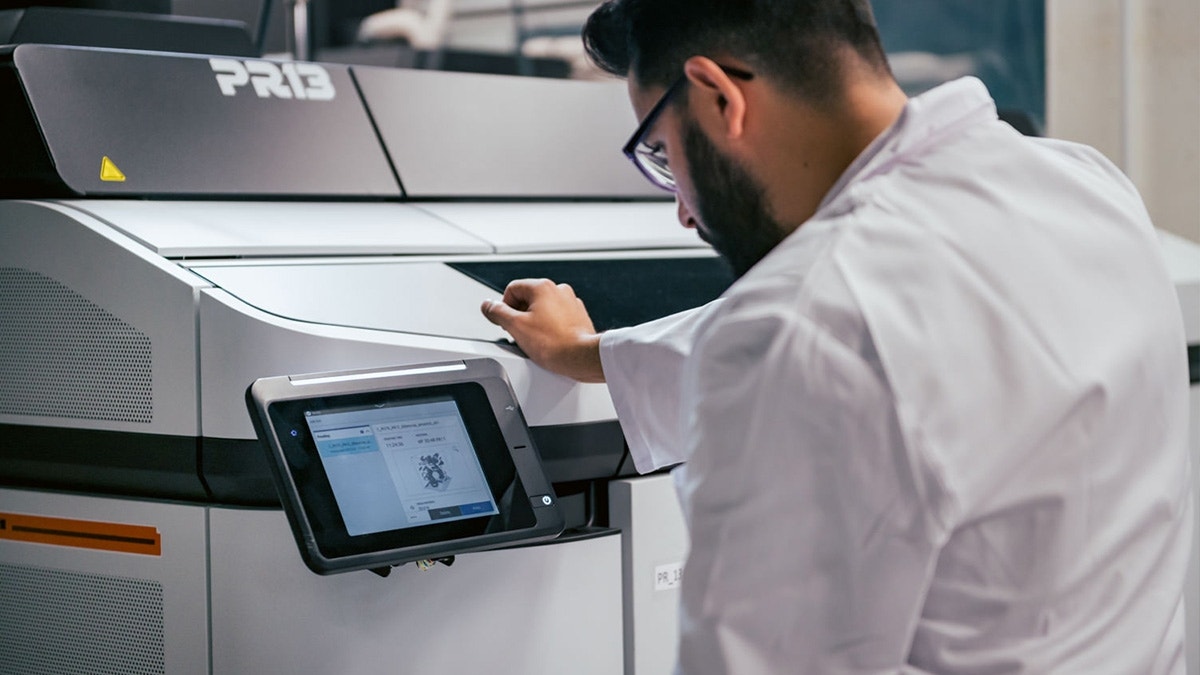