Back in November of 2023, I covered the launch of the FX10 Composite 3D printer – the next-generation industrial machine from Markforged. Sporting enhancements such as a heated build chamber, a precision-machined self-leveling print surface, and automatic material changeover, the FX10 was brought to market as one of the most advanced machines Markforged has to offer.
At the time, Markforged was also positioning the printer as a modular system capable of being easily upgraded to accommodate new printing options and capabilities. At IMTS 2024, Markforged unveiled the first round of these upgrades – a swappable print module that allows the FX10 to also print metal parts. This ability to print both composite and metal parts on a single printer allows for levels of versatility that have previously been available only when using multiple dedicated machines.
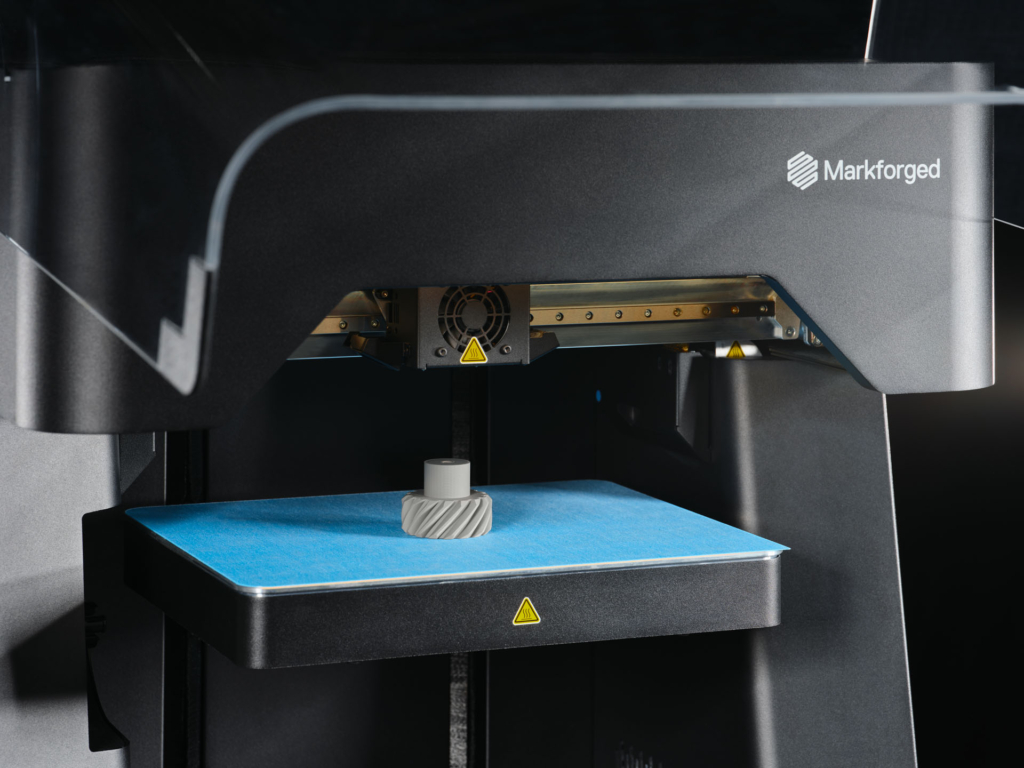
The Science Behind Metal Printing
For anyone familiar with the Markforged ecosystem, the FX10 can print metal parts using the same technology present on the Metal X. Both printers initially create parts using a filament spool of metal powder that is bound by wax and polymer. Like Metal Injection Molding (MIM), geometry off the printer is referred to as green state – in this state, parts are much more fragile compared to their final metal form. Green state parts are washed in a debinder to remove most of the wax and are then sintered to fuse the metal powder together. Once the sintering process is complete, parts are fully metal and can be further post-processed or directly put to use.
Because the actual printing process is extrusion-based, we have seen a lot of customers with experience in similar systems (Markforged or otherwise) jump into this style of metal printing without issue.
Why Can’t I Use Metal Filaments on Just Any Printer?
Since the announcement of this metal module upgrade, a common question that we have received has been, “Why am I unable to take these metal filaments and use them on other printers?” The answer to this is both straightforward and complex – it all comes down to material science.
When Markforged initially entered the space of metal 3D printing, their first-generation metal filaments were extremely fragile at room temperature and required a heated build chamber to print successfully. Even with a heated build chamber, these filaments required a completely straight path to the print head to prevent the filament from snapping.
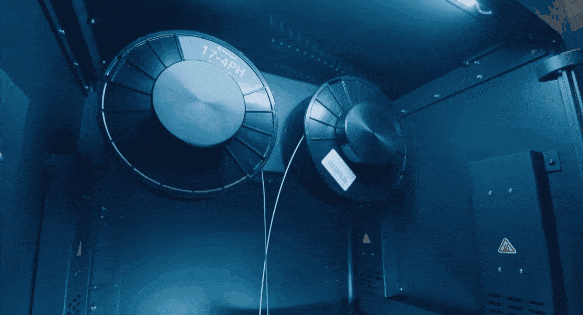
Over the years, Markforged has released more flexible versions of filaments, including 17-4 Stainless Steel and Copper. Compared to their predecessors, they can withstand more bending action before snapping. Despite this, these raw metal filaments will never be as tough as their plastic counterparts. This means that a material pathway with shallow bends and extruder motors with specialized extrusion profiles are still required. A heated build chamber is also needed for the material itself to print geometry successfully. The FX10 was specifically designed with all these metal printing requirements in mind, which is why it is now able to act as one of the most flexible 3D printers to date.
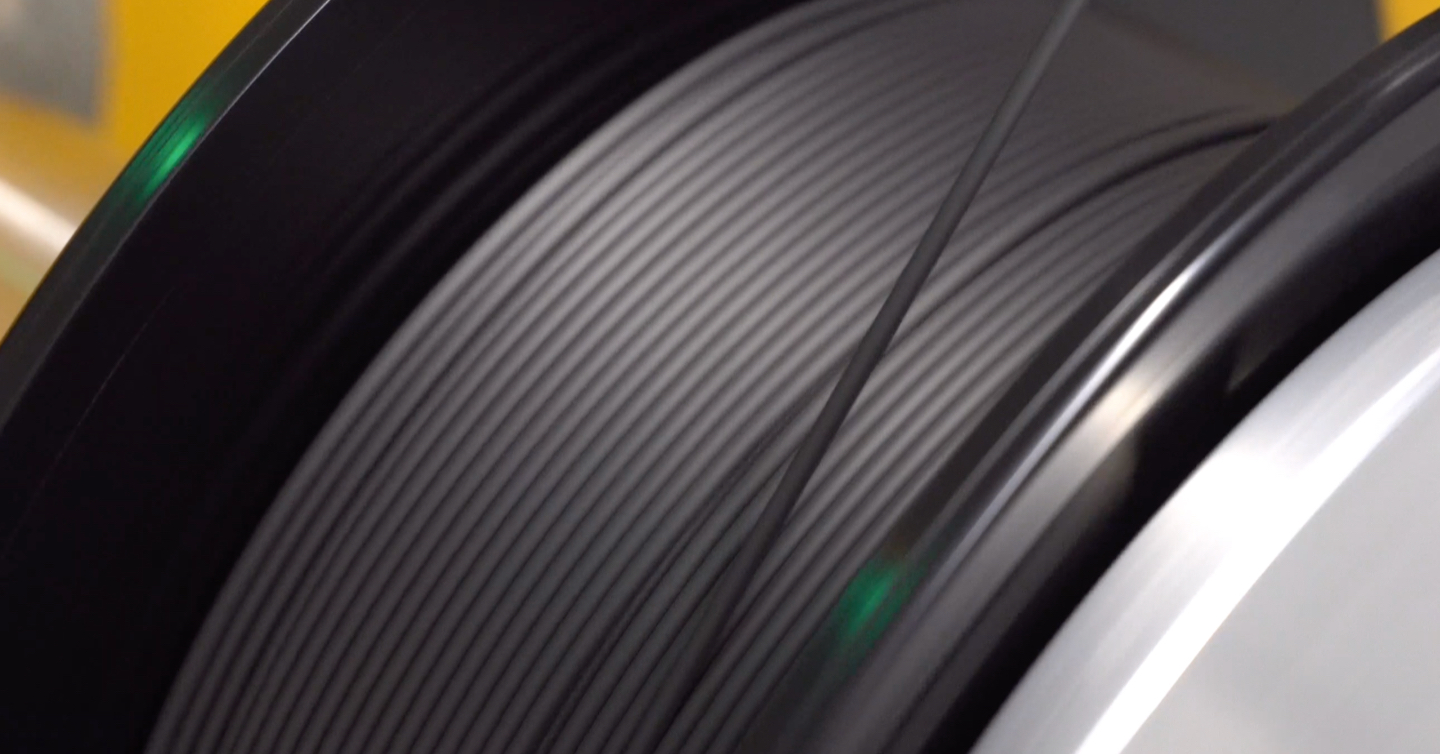
How Easy Is It to Switch Between Composite and Metal Printing?
Like many other tasks on the FX10, Markforged designed the FX10 metal kit with simplicity and ease of use in mind. The conversion between composite and metal printing requires three changeovers – the print head, the material routing block, and the material tubes. Converting the printer involves three simple hardware changes:
- Swap the Print Head – The print head is easily removed by disconnecting the wiring harness and removing two screws.
- Replace the Material Routing Block – Just undo two screws to change this part for handling different materials.
- Change the Material Tubes – Push-to-connect fittings allow quick swaps for material tubes.
While this may sound like a potentially time-consuming task, the entire swap process is estimated to take around 15 minutes. An FX10 print head can be quickly removed from a printer by unhooking its primary wiring harness and removing two captive screws. Similarly, the material routing block that accounts for differences in printing materials can be quickly removed by undoing two screws. Lastly, the material tubes are quickly removed via the push-to-connect fittings on both ends. Once the hardware is swapped out, the printer runs through an automated utility to ensure it is ready for printing with the current setup.
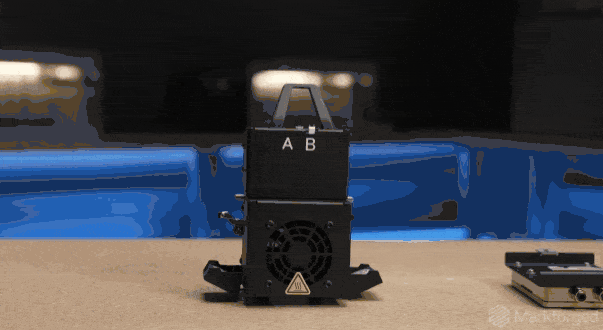
This conversion between composite and metal printing modes is not permanent and can be done as many times as needed. At the time of writing, Markforged does not expect users to perform this swap multiple times a week – rather, it is theorized that operators will run through a queue of several metal parts before swapping back to composite materials.
That’s So Metal: Why Both Composites and Metals Matter in 3D Printing
There have been some massive advancements in the 3D printing space over the past few years, and the ability to print with both composites and metal on a single machine can absolutely be counted as one of these advancements. After all, even though Markforged composite systems can print metal-replacement parts, some parts do just need to be made of metal. This could be due to factors such as thermal requirements, abrasion resistance, or even conductivity.
Here are just a few applications where metal might be the better material choice when 3D printing:
- High Temperatures: Metal parts can withstand heat that composites can’t handle.
- Aesthetic Reasons: You might make a prototype with composite materials, but if you’re making something like a pocket knife, you would want parts of the knife printed in tool steel.
- Abrasion Resistance: Metals offer superior durability in abrasive environments.
- Electrical Conductivity: For parts that need to conduct electricity metal is essential.
The FX10 ensures that users can adapt to changing applications, rather than needing to adopt a new printer or work within the boundaries of a single machine.
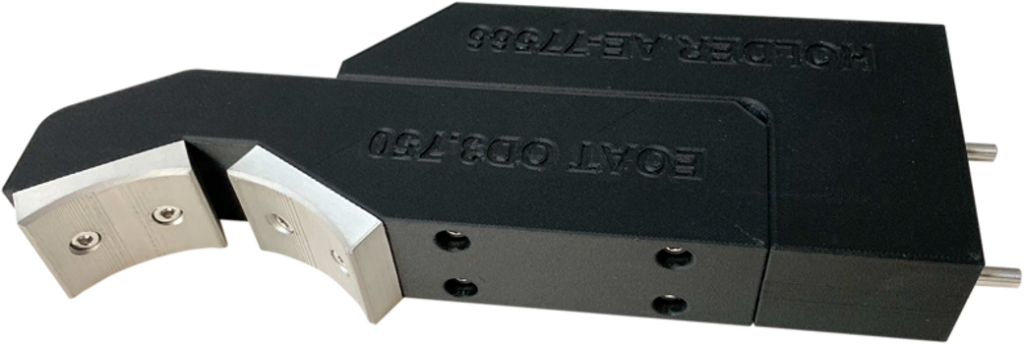
Whether you’re prototyping, manufacturing, or innovating, the FX10 provides the adaptability you need to meet a wide range of challenges without requiring multiple printers.
If you’d like to learn more about the FX10 metal module release, feel free to watch our webinar on the topic. Also feel free to contact us today if you’d like to talk about the FX10 or anything else 3D printing related.