Metal 3D printing — or additive manufacturing — enables the creation of complex, customized metal parts with unique geometries not possible with traditional manufacturing. If you’re a manufacturer or engineer, understanding the potential of metal additive manufacturing and the various types of metal printers can help you cut costs, and in some cases, create parts in a more sustainable way.
That begs the question — is metal 3D printing actually sustainable? It may be too early to tell just how sustainable (or not) metal additive manufacturing actually is, according to a 2020 literature review from the Additive Manufacturer Green Trade Association.
Compared to traditional manufacturing methods, metal 3D printing offers significant advantages in creating strong, durable products with complex geometries, and in some cases, saves on material and energy costs. It comes down to energy usage, material recyclability, and many other factors.
If you’re not sure if metal 3D printing is the most sustainable choice for your part or product, you can create a lifecycle assessment to compare metal additive manufacturing to traditional manufacturing methods.
Generally, since metal retains properties and quality during recycling more easily than other additive manufacturing materials like composites, it’s a more sustainable material choice. And in industries like aerospace, where lightweighting parts must happen, choosing metal materials turns out to also be a more energy-efficient choice.
In this article, we’ll cover metal 3D printing technologies, applications, and best practices.
What Is Metal 3D Printing and Who Uses It?
Metal 3D printing, also known as metal additive manufacturing, fuses metal particles using high temperatures derived from lasers or electron beams.
One of the methods used in metal 3D printing is electron beam melting. This process creates metal objects by sintering, melting, or welding layers of metal or metal powder until a part is complete. It’s a method that offers unparalleled flexibility in design and manufacturing.
Metal 3D printing produces metal parts at scale, achieving industrial overall equipment efficiency and reduces manual labor with automation. It reduces production costs, shortens design cycles, and enables the creation of strong, durable products with complex geometries and specific customization requirements.
Top Applications in Key Industries
Metal 3D printing applications vary across industry. In healthcare, think medical devices like patient-specific hip and knee replacements. And in consumer products, metal 3D printing is used to create custom items like jewelry and eyewear.
While you’ll see many industries 3D print metal, it’s most heavily used by the aerospace and automotive industries.
Aerospace Industry
There are unique benefits for using metal 3D printing in this sector — producing lightweight, complex components, such as engine parts and satellite components. The ability to create intricate designs and reduce weight without compromising strength is invaluable.
It’s estimated that using lightweight metal additive manufacturing materials like aluminum, nickel, titanium, and steel alloys can save over 100 million metric tons of carbon dioxide through the year 2050 because of a 6.4% fuel reduction.
For example, Relativity Space uses metal 3D printing to create up to 85% of the body of its rockets, and also engines. It utilizes wire arc additive manufacturing (WAAM), which is a type of direct energy deposition (AKA laser metal deposition.)
And Stargate, the world’s largest metal 3D printer and currently at Relativity Space’s facility, uses a high-powered laser, plasma arc technology, autonomous robotics, and AI with the goal to make rockets with 100 fewer parts in less than two months.
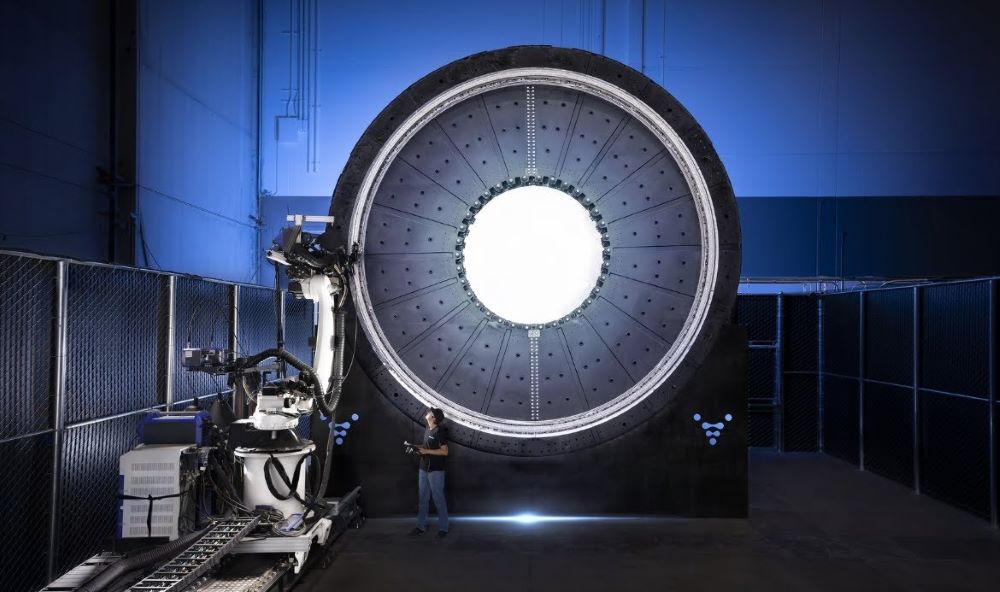
Automotive Industry
The automotive industry 3D prints metal to produce custom car parts, such as engine components and exhaust systems. This technology allows for rapid prototyping and production of high-performance parts.
Ford, the well-known automotive brand, reduces its expenses by up to 80% compared to traditional manufacturing methods using 3D printing.
Not only does this support its sustainability initiatives through material reuse, it also is cutting down the time it takes to create parts and components used in its vehicles. Ford used metal additive manufacturing to create things like aluminum intake manifolds for the engines of the Ford F-150 model.
5 Types of Metal 3D Printing Methods
Not all metal 3D printing is the same. There are a few differences between the various types of metal 3D printing processes available.
Here’s a brief overview of the various methods:
- Direct Metal Laser Sintering (DMLS): Uses a laser powder bed fusion process to fuse metal powders together, layer by layer, to create complex geometries and structures. This technology is ideal for producing highly detailed and precise metal parts.
- Powder Bed Fusion: Utilizes technologies like direct metal printing (DMP) and laser powder bed fusion. Electron beam melting is a popular method within powder bed fusion. It employs a laser or electron beam to fuse metal powders together, layer by layer, creating intricate geometries. Selective laser sintering (SLS) and electron beam melting (EBM) are popular methods within this category.
- Direct Energy Deposition: Also known as laser metal deposition, this process uses a laser to melt and deposit metal feedstock onto a substrate, layer by layer. This approach is excellent for creating complex structures and repairing existing components.
- Binder Jetting: Metal binder jetting employs a liquid binder to fuse metal powders together, layer by layer. The process includes distributing metal powder, applying a binding polymer, and performing a post-processing step called “sintering” to create fully metallic parts.
- Bound Powder Extrusion: Similar to metal injection molding, this method uses bound metal powder extrusion material, which is safer and easier to use than loose metal powder. Markforged Metal X is a good example of this technology.
When to Choose Metal 3D Printing Over Traditional Manufacturing
Metal additive manufacturing offers greater design flexibility, reduced material waste, and faster production times compared to traditional manufacturing methods. It’s highly advantageous for mass production due to its efficiency and scalability, making it ideal for OEMs and component suppliers to 3D print quality metal parts at scale.
Metal, for the most part, is also easier to recycle than other types of materials.
Metal additive manufacturing is perfect for producing complex geometries, custom parts, and small batches. It’s also highly effective for rapid prototyping and production, offering a versatile solution for various manufacturing needs.
Top Metal 3D Printers and Material for Businesses
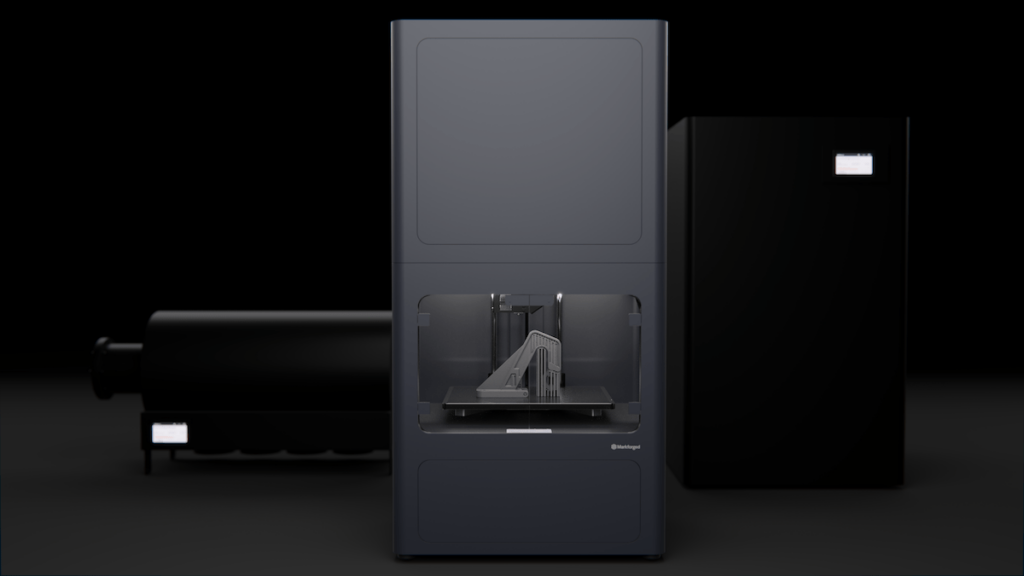
Leading metal printers include HP Metal Jet, Markforged Metal X, and more. These advanced machines use various materials, including cobalt chrome, known for its excellent wear and corrosion resistance, high hardness, and biocompatibility.
The Markforged FX10 is also capable of printing both metal and composites. For more information, watch our webinar on how you can metal print with the FX10, or read our article on why you should metal plate your parts.
When it comes to material selection, there are many factors to consider like strength, corrosion resistance, and thermal conductivity. Metal powders are used in the majority of metal 3D printing technologies. The quality and properties of the metal powder significantly impact the final product.
Here are some of the top metal 3D printers available and which materials they can utilize:
- HP Metal Jet: Print using materials like HP Metal Jet SS 316L, HP Metal Jet SS 17-4PH, IndoMIM M2 Tool Steel, Osprey® 316L, GKN 17-4PH, GKN Free Sintering Low Alloy Steel, GKN M2 Tool Steel, GKN 316L, and GKN Nickel Free Stainless Steel.
- Markforged Metal X: Print using materials like 17-4 Stainless Steel, H13 Tool Steel, A2 Tool Steel, D2 Tool Steel, and Inconel 625.
- Markforged FX10: Print using materials like 17-4PH Stainless Steel, Copper, H13 Tool Steel, Inconel 625, A2 and D2 Tool Steel, and Bound Powder Metal Filament.
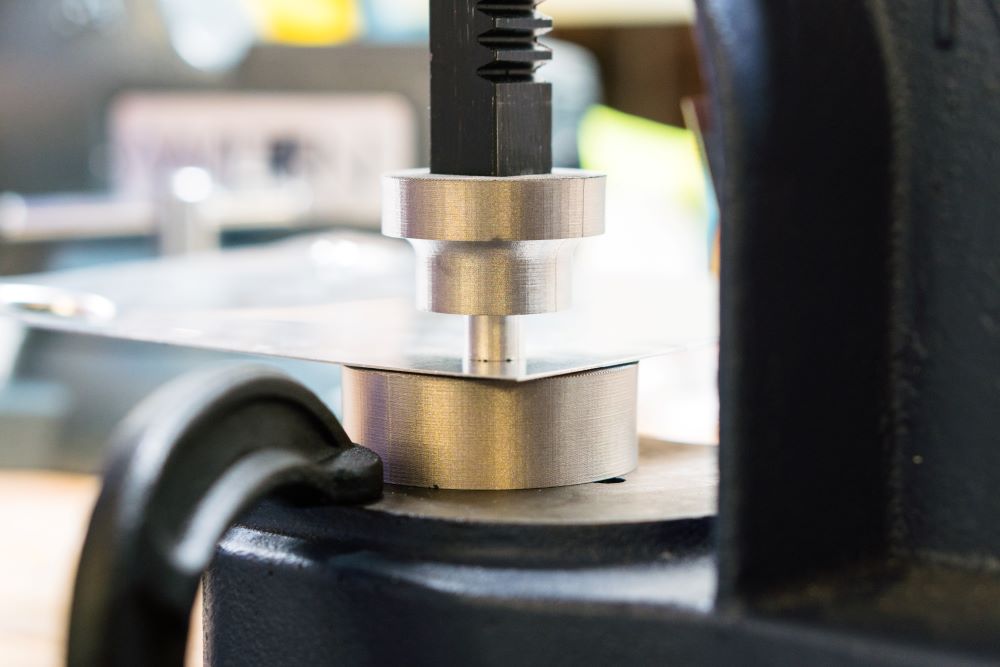
Other Considerations
Metal additive manufacturing is crucial in various industries due to its performance, repeatability, and precision in the production of metal components, but there are still many things to consider like understanding and utilizing software, optimizing the print bed layout and figuring out what kind of post-processing techniques are needed.
Not only that, but you also need to carefully consider the selection of materials, how to optimize your print parameters, and design workflows that ensure quality.
Post-processing Methods
Post-processing in metal additive manufacturing includes machining, grinding, and polishing to achieve the desired finish and properties. Handling and recovery of loose powder during post-processing is crucial, involving various techniques to manage and utilize the powder effectively.
Support Structures and Part Orientation
Support structures and proper part orientation are critical for ensuring successful prints and minimizing material waste in metal additive manufacturing. These elements help maintain the integrity of the printed parts during the manufacturing process.
Getting Started 3D-Printing Metal
Choosing the right metal 3D printer for your business needs involves considering factors, such as print resolution, build volume, material compatibility, and post-processing requirements.
Metal additive manufacturing offers numerous benefits, from design flexibility to cost-effective production at scale. It’s a significant advancement in manufacturing technology used by leading manufacturers and military institutions.
Considering going metal? Reach out to us to get metal 3D printing expert advice and to learn more about how it can benefit your business.