Sustainability should be an area of focus from a product’s conception, throughout the design phase and even beyond when considering environmental impacts.
When considering sustainability from the start, costly design changes can be avoided, especially as the design constraints increase.
With advanced simulation design exploration tools like optimization and topology analyses, not only can designs meet specific standards but innovation is easily achieved.
Combining these techniques with efficient lifecycle assessment studies, a product can be designed in a way that optimizes its manufacturability and strength while minimizing its environmental footprint.
How Optimization & Topology Analyses Support Sustainability
A common way of incorporating sustainability in product design is reducing a product’s mass. Less mass means less material, which will, in turn, reduce that product’s footprint.
The two main ways of doing this are optimization analysis and topology analysis. Both techniques use constraints to define what can and cannot change, whether it be certain dimensions that will vary in an optimization study or specific regions that must remain the same in a topology study.
They also implement the use of goals to define the overall objective of the analysis. This ranges from minimizing mass, creating the best stiffness-to-mass ratio, or aiming to minimize or maximize the resonant frequency.
What’s the Difference Between Optimization & Topology Analyses?
The main difference in optimization and topology studies is the result.
An optimization study will yield parametric results based on the dimensions that were chosen to be changed based on the constraints, while a topology study yields a more organic, nonparametric result.
Topology studies not only allow the users to meet design constraints but are a great way to drive innovation. Maybe ribs are added in places that were not once considered, or material is removed in a way that was not obvious at first.
Because of the shape of the topology results, these studies are ideal when 3D printing is the planned method of manufacturing.
Here are examples of a topology study:
- Initial Design
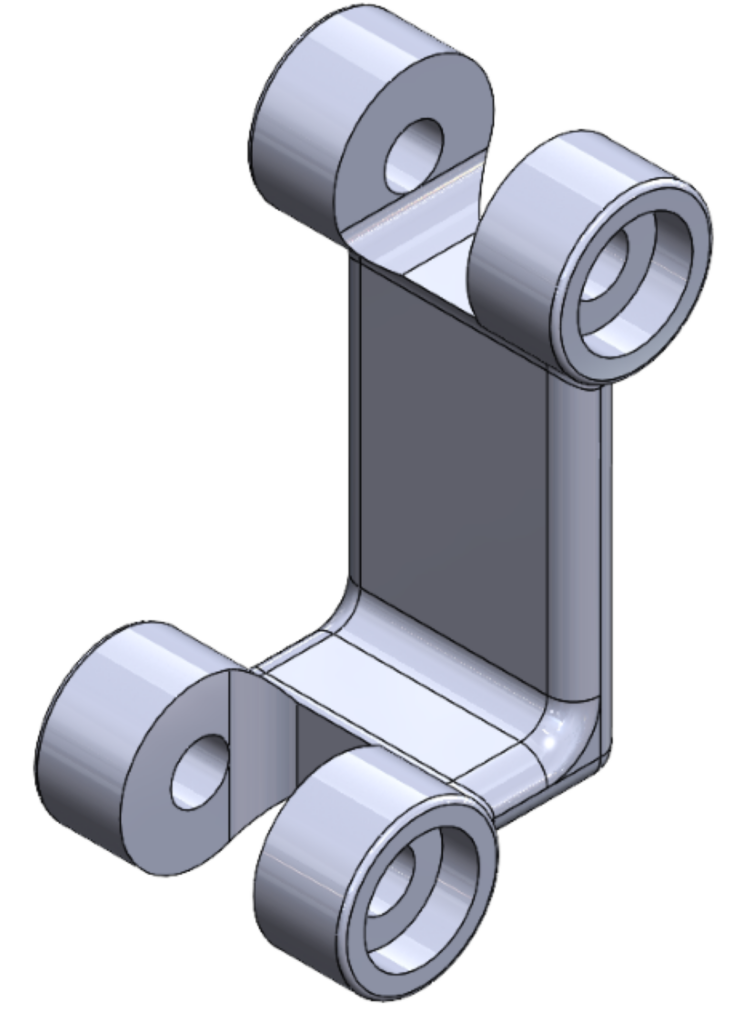
This is an initial design of a bracket that an engineer wants to optimize with topology. The designer knows how and where the bracket will be secured into place, as well as the direction and size of forces that it will undergo during its usage, and the desired factor of safety (FOS) value that needs to be achieved.
2. Topology Study Results
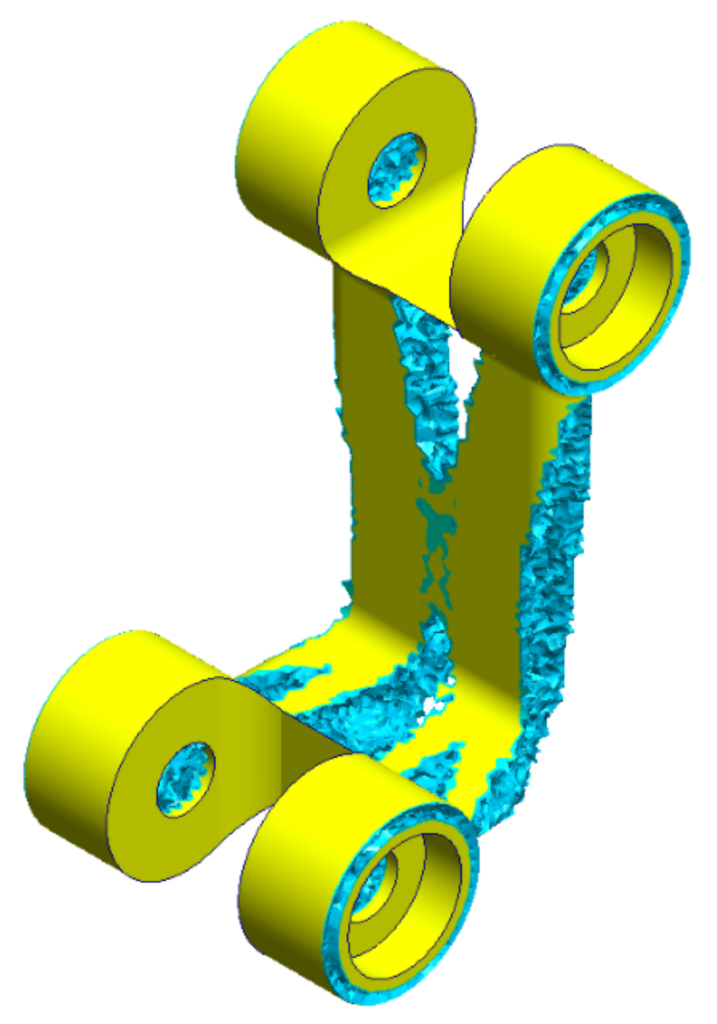
The part was restrained inside of the top counterbore holes, and a vertical force of 60 lbs was added to the lower counterbore holes.
By inputting that data into a SOLIDWORKS topology study parameters, along with a desired FOS > 2, a result is created that shows the user areas of geometry that can be removed. It can still be manipulated to add or remove material in areas where it is not needed.
3. Exported Mesh Used to Model New Design
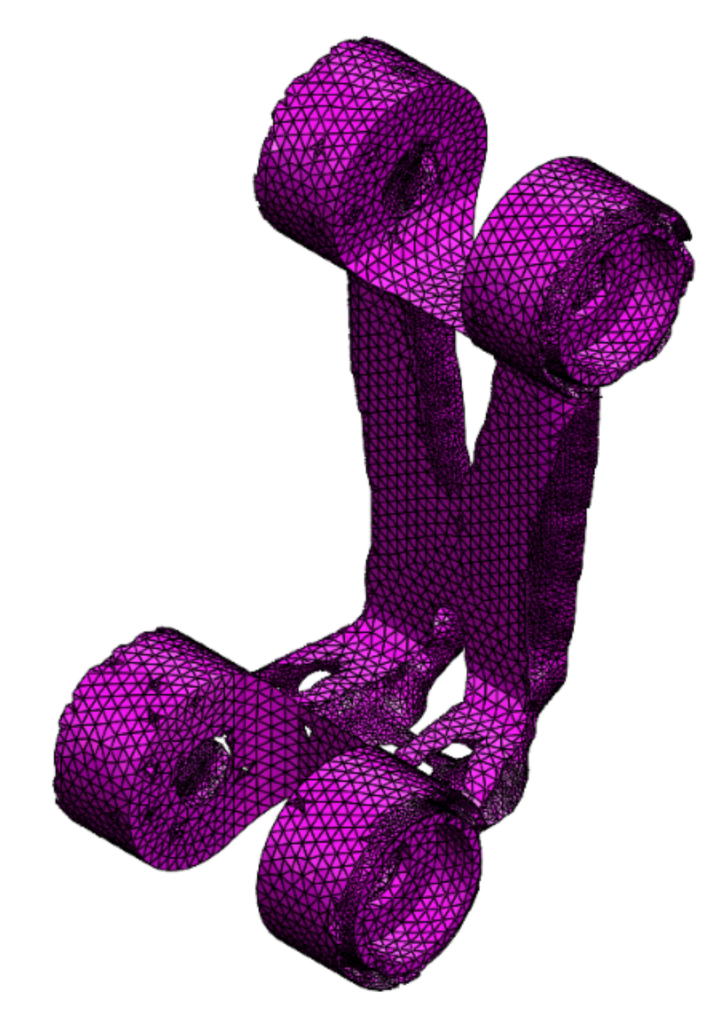
The original part has now been converted into a preview of a mesh body. The designer then removes enough material to find a nice balance between form and function, then it is exported as a mesh body.
4. New Design Based on Mesh
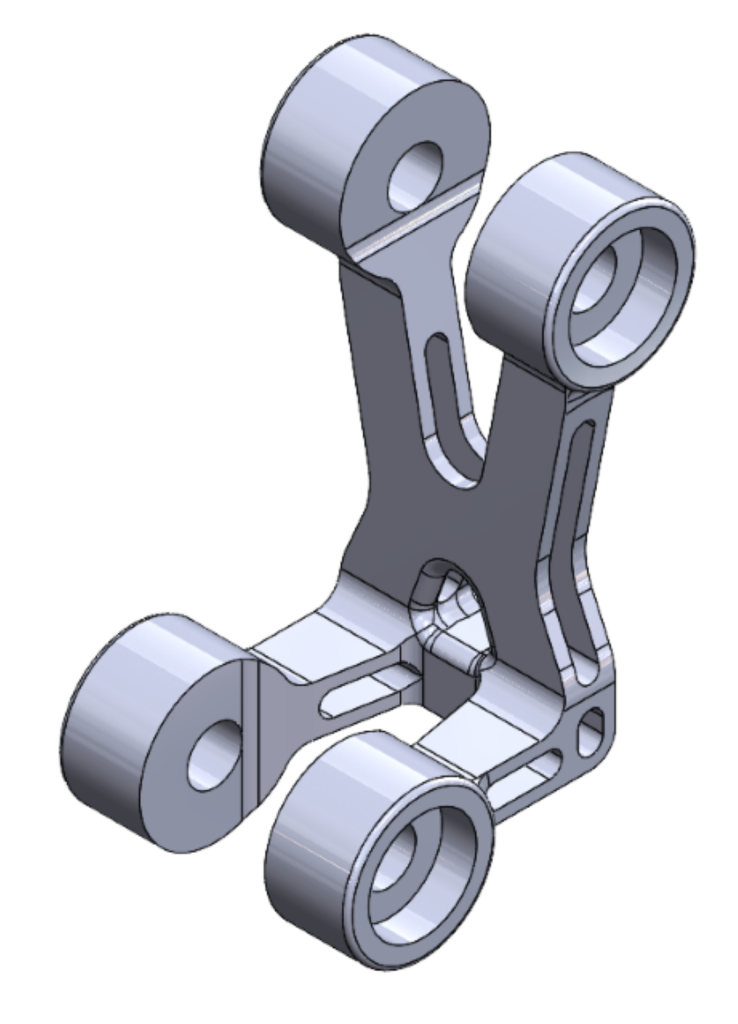
That mesh body is used as a guide to make changes to the original design. Locations where material can be removed without affecting any design constraints have been taken into consideration and worked into this new design based on the topology study results.
5. Simulation on New Design
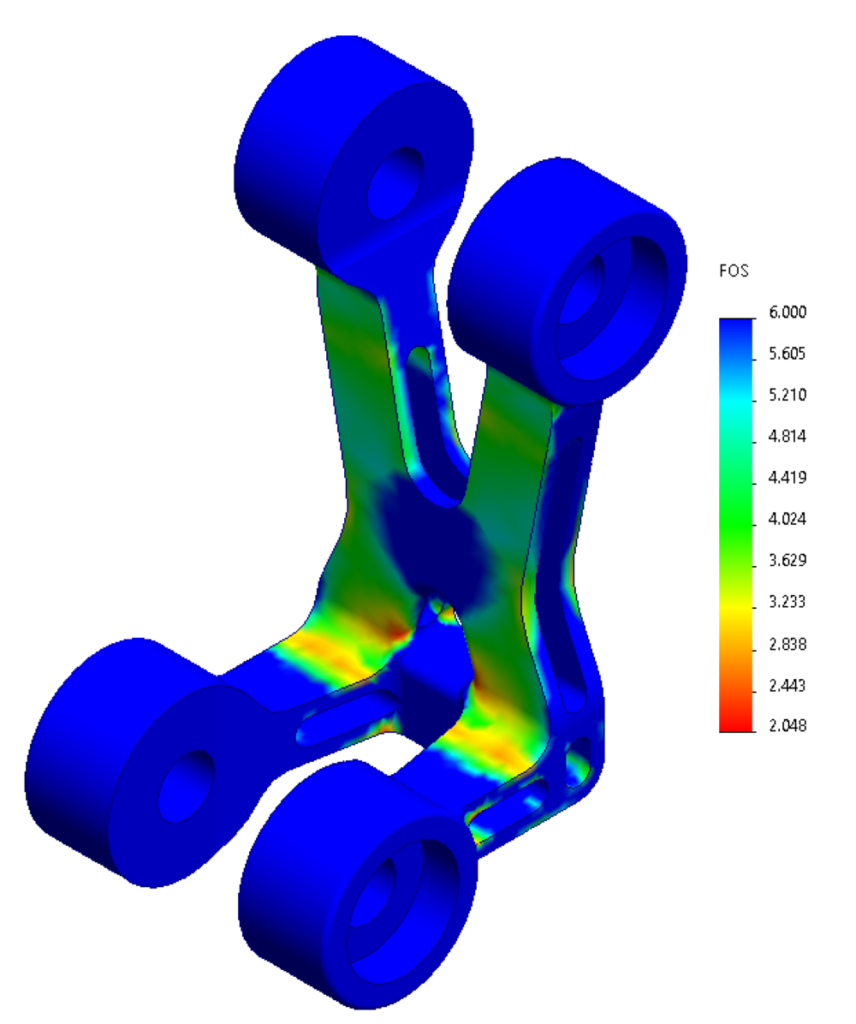
To confirm that the innovative new design will still be adequate, we run a linear static simulation to make sure that it can withstand the original forces. The image shows the updated design model to confirm FOS > 2. The minimum FOS is 2.048.
6. Topology Optimization Workflow Before Simulation
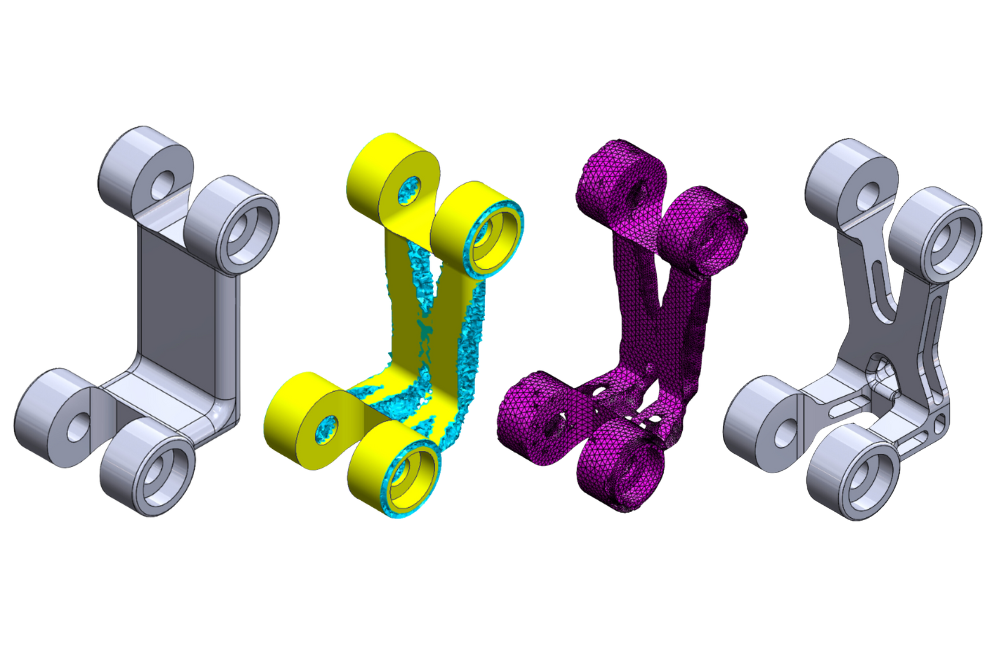
Without first running a topology study, coming to the final design could have been a lengthier process and required several trials of physical testing and prototyping.
Reducing Waste with 3D Printing
3D printing offers several benefits when it comes to sustainability. Since 3D printing is an additive process, less waste is produced when making parts compared to traditional subtractive processes like milling or turning.
These traditional processes produce a lot of material waste, which then must be shipped to disposal facilities, further increasing energy waste and decreasing sustainability.
An estimated 292.4 million tons of waste ended up in landfills in 2018, which is enough energy to power every home in the United States for over a month.
Alternatively, 3D printing only uses enough material to make the part, so waste and the need to ship that waste is dramatically reduced.
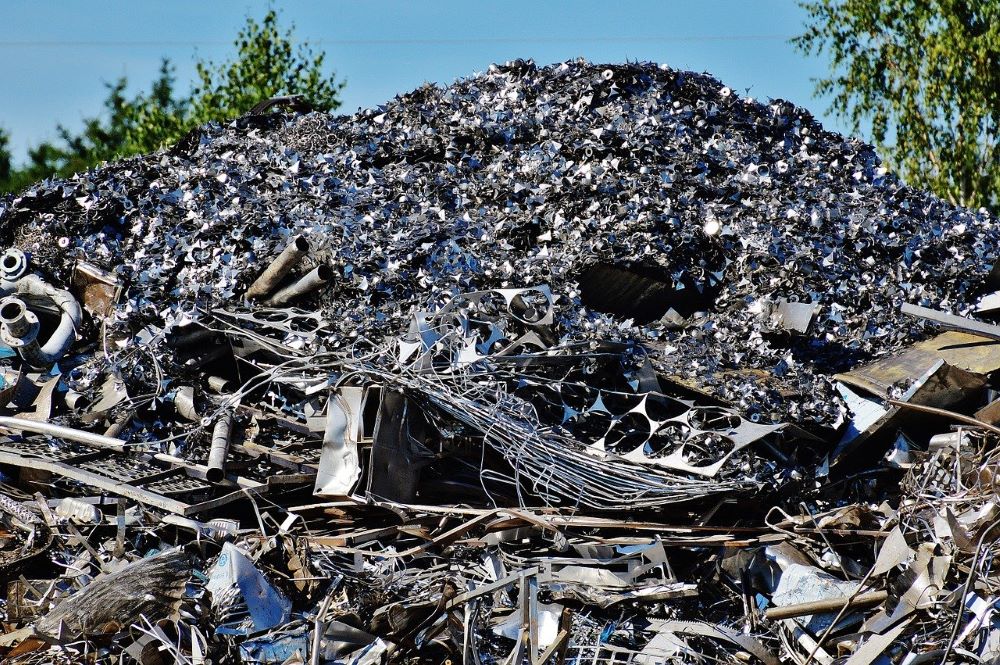
Creating Non-Solid Parts with Infill
Another way that 3D printing decreases material usage is by creating non-solid parts that have a sparse infill compared to their traditional counterparts.
The inside of the part is printed with a lattice structure instead of being completely solid, which decreases the material needed to create the part, speeds up production, and offers opportunities for light weighting.
A part made with a subtractive process might look the same as a part made from an additive process, but internally the structures could be different leading to reductions in part mass and therefore increases in sustainability.
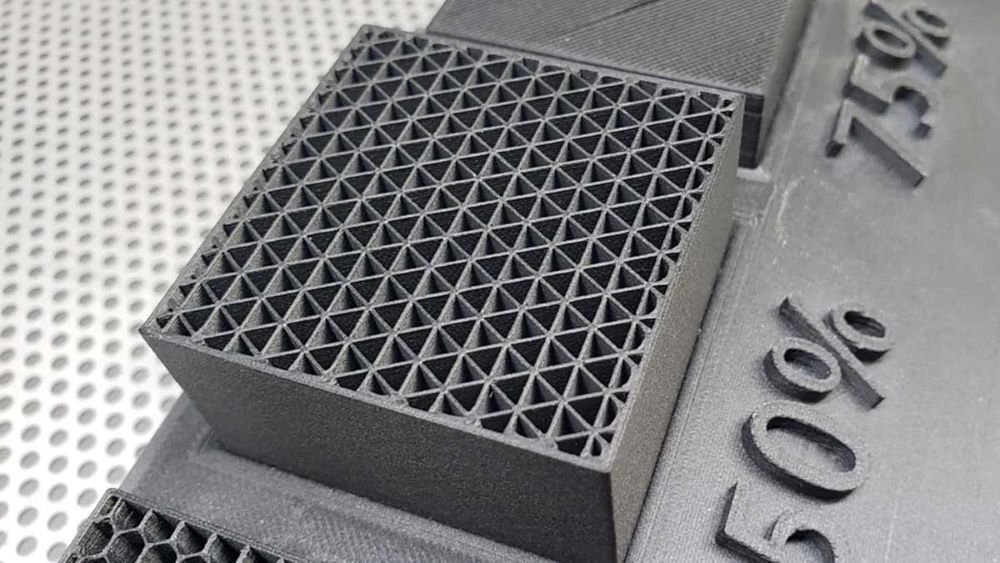
Why Choose 3D Printing Over Traditional Manufacturing for Sustainability?
Every manufacturing process has its limitations and advantages, and 3D printing is no different.
One advantage is that additive processes can create part geometry that might not be possible using traditional methods.
For example, using 3D printing, it’s easy to make a part that has complicated internal channels while with traditional manufacturing you can only drill channels in a straight line. This means that you might be able to make parts with complicated geometry produced by topology that increase the life of the part, reduce its mass, and improve its function.
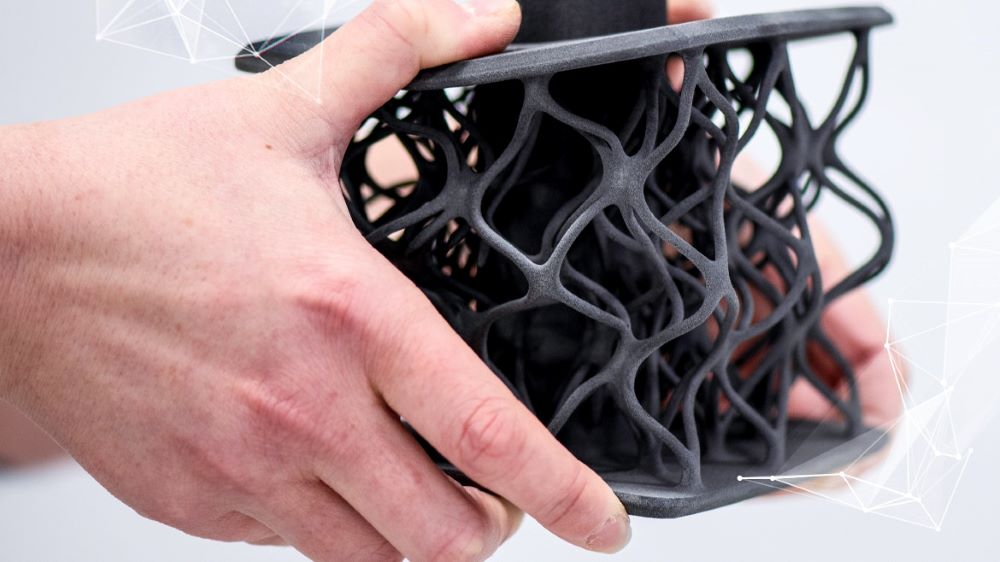
How SOLIDWORKS Evaluates for Sustainability
When designing a product for sustainability, there are some questions that need to be considered, such as:
- Based on the product and manufacturing process, what will the environmental footprint look like?
- Although the new design appears to be more eco-friendly, does this hold true when considering all lifecycle phases?
- How are the manufacturing locations and shipping costs balanced with the costs of a sustainable design?
- What is the largest contributing factor to the environmental footprint?
The SOLIDWORKS Sustainability add-in and the Eco-Design Engineer role through the 3DEXPERIENCE platform are designed to help answer these.
Once multiple designs have been established, their environmental impacts can be evaluated using these tools. This will then show the design’s key properties like how it would affect global warming through CO2 emissions, acidification, carcinogenic effects, respiratory effects, and freshwater ecotoxicity, just to name a few.
The recyclability of a product can be tested, and even more importantly, the end-of-life disposability can be modeled. These desired environmental targets can then be used to drive sustainable design by assessing these, and more, environmental metrics.
The SOLIDWORKS Sustainability add-in can be used to quantify the overall environmental impact as well as the difference between the initial and final designs.
Using known data (such as the type of material, the manufacturing and intended use locations, the method and length of travel, and the duration of use), the software will be able to give a comparison chart looking like what is shown below.
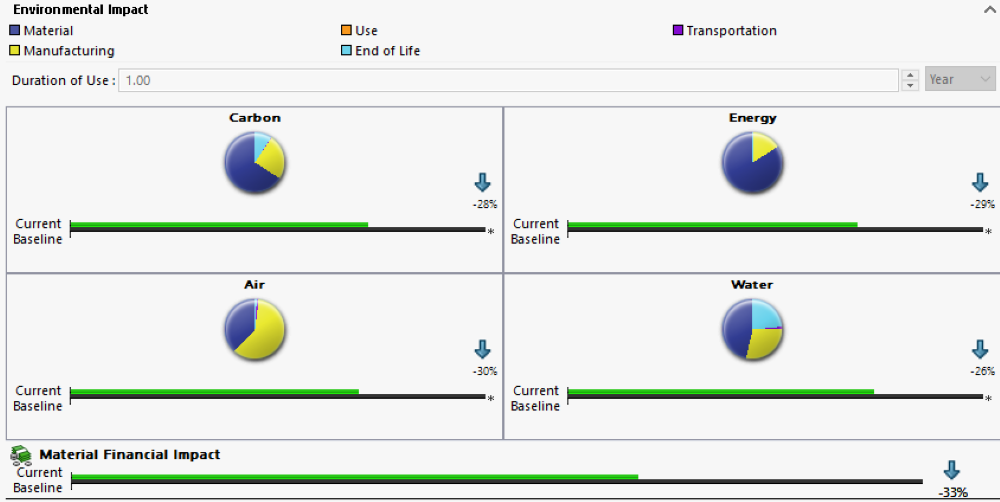
A report can also be created showing more precise values of these environmental impact values. The results above use the initial and new designs from the topology optimization example found in the “What’s the Difference Between Optimization & Topology Analyses?” section.
The Final Note
As industries increasingly prioritize sustainable design, 3D printing and innovative materials continue to pave the way for a more eco-friendlier future.
By leveraging these technologies, businesses can reduce waste, optimize material usage, and create products that align with environmental goals.
Ready to explore how sustainable design can enhance your projects? Connect with our experts today to learn more