Additive manufacturing demands post-processing solutions that are precise and highly adaptable. The DyeMansion Powershot X addresses these needs with a sophisticated design that offers flexibility, performance, and efficiency. Officially launched at Formnext 2024, this advanced system redefines post-processing workflows, providing manufacturers with a reliable solution for scalability and consistent quality.
The Powershot X stands out as a multi-functional system capable of running three distinct processes within a single platform:
- PolyShot Cleaning (PSC), which effectively removes powder residue from 3D-printed parts
- PolyShot Surfacing (PSS), designed to enhance surface finishes for a smooth, homogeneous look
- PolyShot Cleaning & Surfacing (PS C&S) process, enabling simultaneous cleaning and surface homogenization
This capability allows manufacturers to consolidate their post-processing operations, reducing the need for multiple machines and ensuring optimal results across a variety of production scenarios.
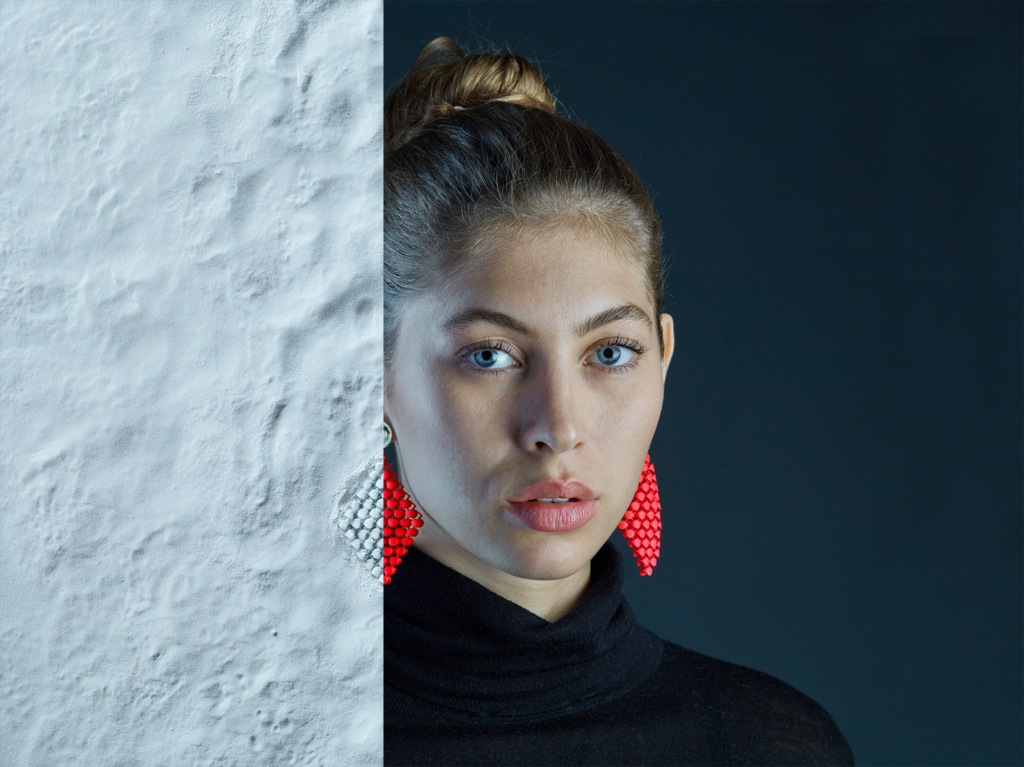
One of the most significant advancements in the Powershot X is its innovative basket and lining design. This feature minimizes particle retention, ensuring cleaner operations and reduces the frequency of maintenance. Additionally, the integration of antistatic injection technology improves the efficiency of cleaning and surfacing processes by reducing powder and media adhesion. The fixed nozzle mount further enhances operational precision by maintaining consistent alignment, ensuring repeatable high-quality results across production runs. For ease of maintenance, the vacuum cleaner interface allows for direct dust removal, reducing operator exposure to particles and helps maintain a cleaner workspace.
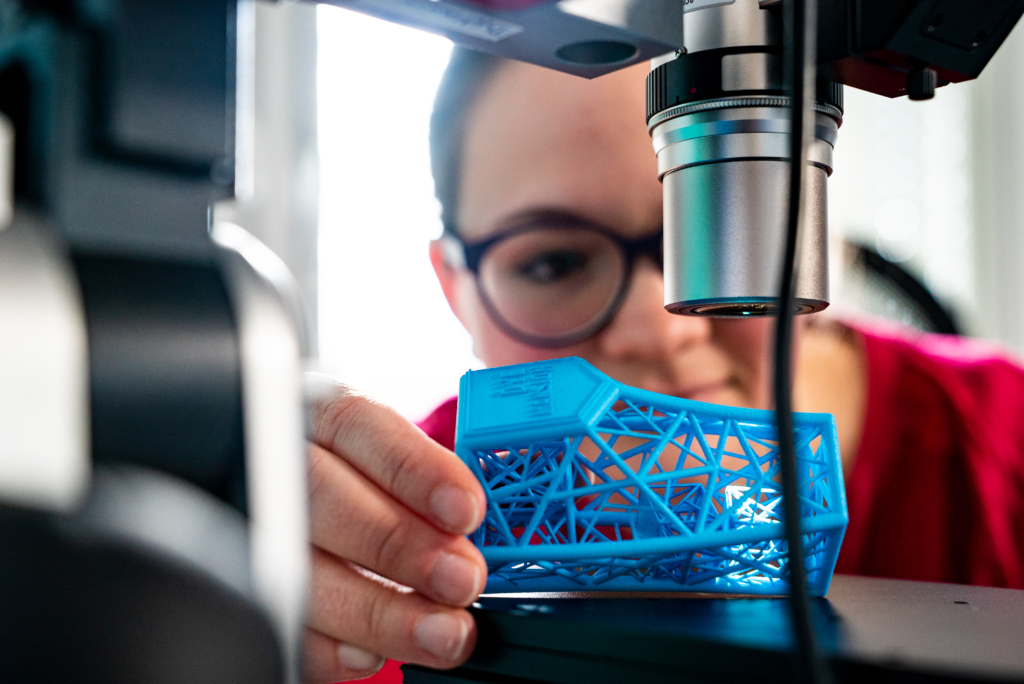
How Long Does the Powershot X Take to Post-Process Parts?
The Powershot X is built for performance and scalability, making it suitable for both small-scale operations and high-volume production environments. Its cycle times range from five to ten minutes for PolyShot Cleaning with glass media to thirty to forty minutes for the combined cleaning and surfacing process. The system supports a wide range of part sizes and geometries, with a capacity to process a single HP Jet Fusion 5200 build per cycle. With a power requirement of 1kW and optimized compressed air consumption, the Powershot X ensures efficient operation while keeping energy costs low.
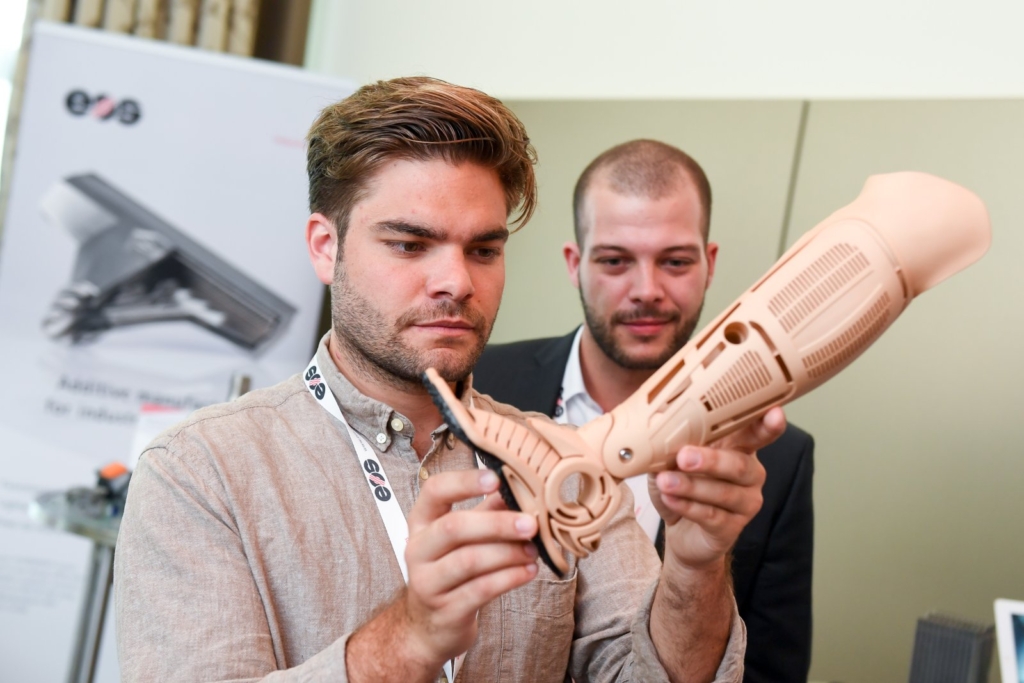
Compared to competing systems like AM Solutions’ S1, the Powershot X offers a more practical approach by focusing on essential functionalities rather than unnecessary features. While competitors may include options such as ATEX compliance or digital pressure settings, these additions often contribute to higher costs without significant benefits for most users. The Powershot X, priced at $43,700, provides a cost-effective solution with low operational expenses, exceptional scalability, and a proven track record in handling diverse part geometries and sizes.
The system was officially launched at Formnext 2024, with shipments starting in February 2025. As part of DyeMansion’s portfolio update, the Powershot S will be discontinued at the end of 2024, while the Powershot C will remain available at a reduced price, offering an economical option for specific applications.
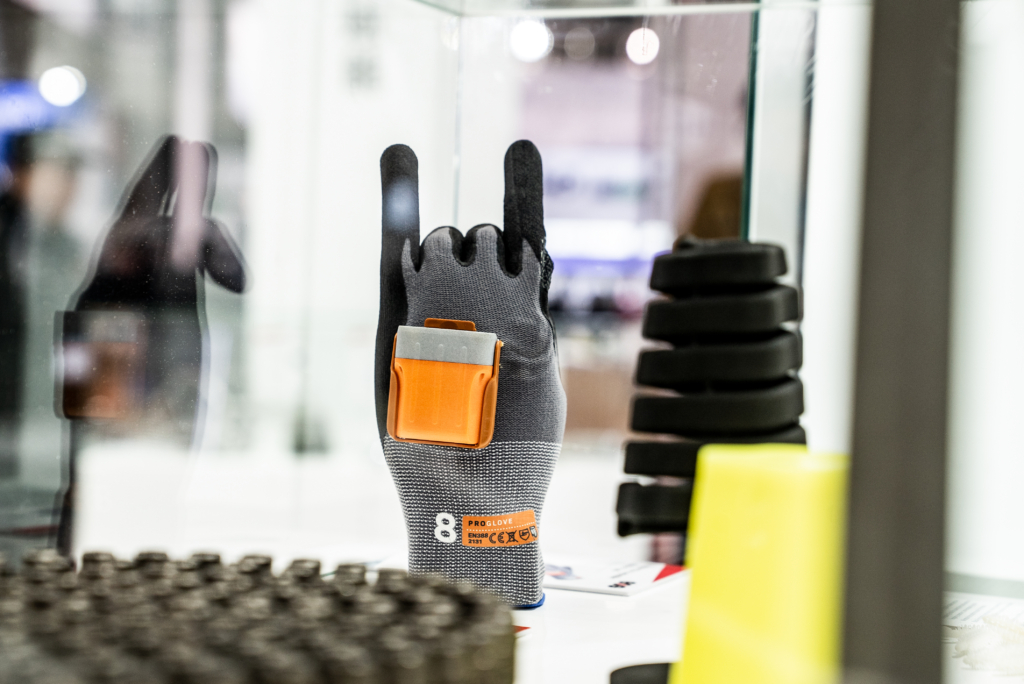
The DyeMansion Powershot X is a testament to innovation in post-processing technology. Its versatility, efficiency, and cost-effectiveness make it a valuable addition to modern additive manufacturing workflows. With its launch on the horizon, the Powershot X is poised to set new benchmarks in the industry, delivering reliable, high-quality solutions for manufacturers worldwide. Learn more about our recommended post-processing systems for additive manufacturing operations.
Want to know more or have specific questions? Reach out to Hawk Ridge Systems.