CAMWorks
Get Pricing Sent to You Today
While you are waiting, check out our Resource Center or read our Blog!
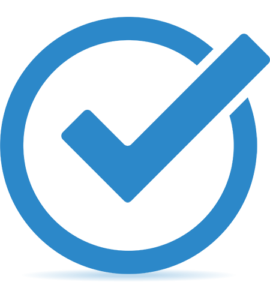
Powerful CNC Machine Tool Programming Inside SOLIDWORKS
CAMWorks offers a seamless process for converting 3D CAD models into CNC parts, ensuring design accuracy across industries by leveraging SOLIDWORKS integration and full associativity, enabling rapid iterations and updates.
With CAMWorks, design changes are effortlessly managed through SOLIDWORKS associativity, triggering automatic toolpath updates and eliminating rework. Additionally, CAMWorks accelerates programming with advanced feature recognition technology and rules-based machining, allowing for efficient part programming and standardized techniques, ultimately reducing cycle times for both milling and lathe operations.
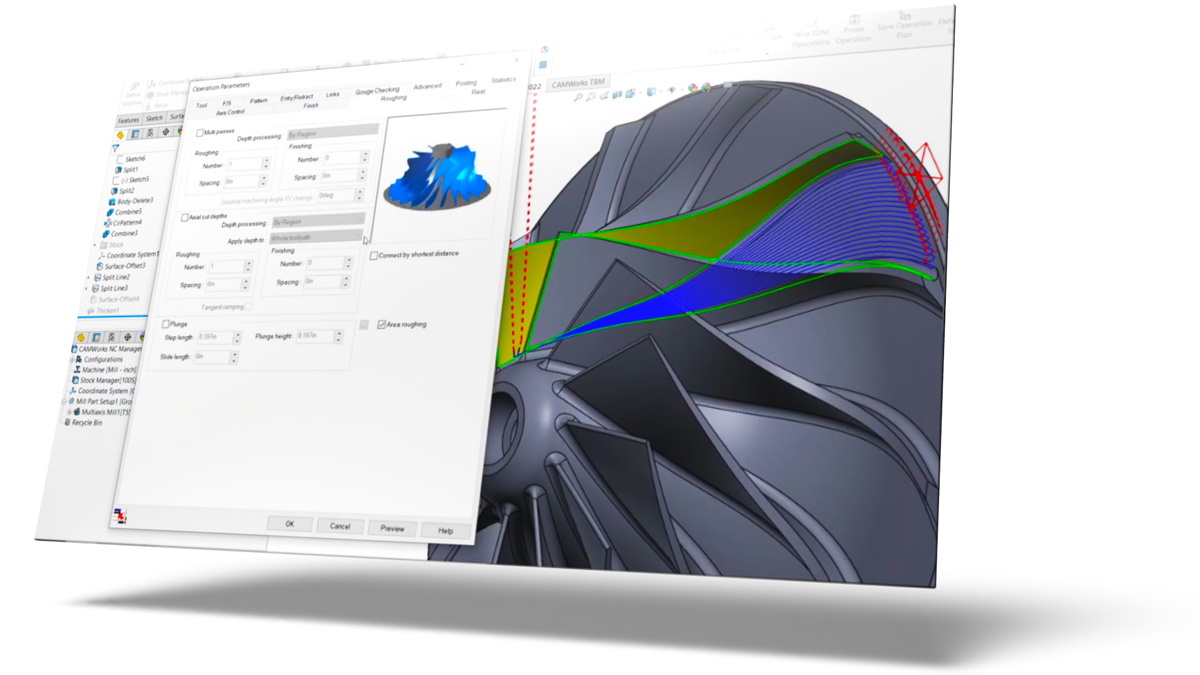
Key Benefits
To compare all CAMWorks packages, download our comprehensive CAMWorks product matrix.
Integrated CAD/CAM
Full associativity between CAD and CAM software means that when the CAD model changes, updates are automatically made to the CAM toolpath, eliminating manual re-work (and the associated errors).
Tolerance Based Machining (TBM)
Minimize errors and inconsistencies by automating the creation of machine programs using tolerances and annotations with the 3D CAD models to select the correct tools and speeds to generate the best toolpath.
Automatic Feature Recognition (AFR)
Automatically recognize machinable features on the CAD model, such as holes and pockets, to eliminate manual work to map out features, reducing programming time.
Knowledge Based Machining (KBM)
Define repeatable machining processes to help accelerate programming.
Custom CAMWorks APIs
Automate and streamline programming processes, based on your specific requirements, through a custom set of defined rules.
Reduce Cycle Times
Leverage the VoluMill technology for high-speed material removal for smoother and faster machining performance.
Pushing the Limits On and Off the Track: RPG Customer Story
RPG Offroad is an automotive company pushing the envelope in vehicle manufacturing by leveraging cutting-edge technology like SOLIDWORKS and CAMWorks. Corey Kausch and the team transitioned from outsourcing expensive machining work to bringing production in-house.
Today, the team has drastically reduced time and costs, streamlined processes with rapid design modifications and maximized tool life for years to come using CAMWorks VoluMill.
Manufacturing Resources
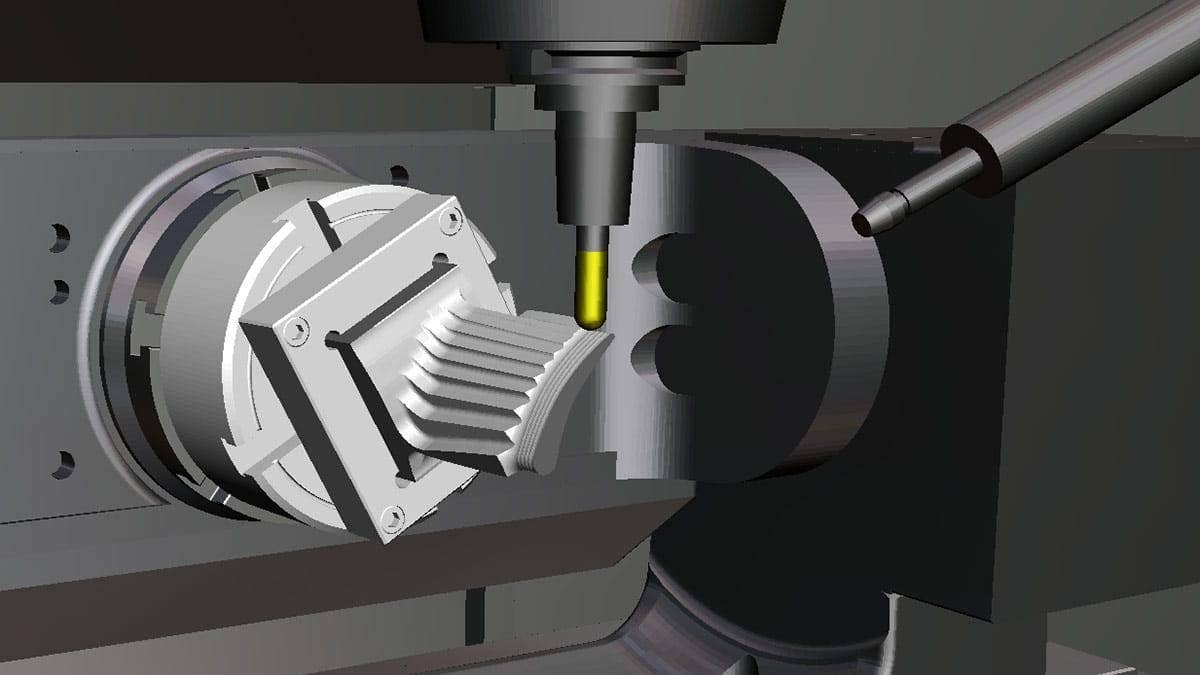
Are Your CAM Tools Working Together? They Should Be.
Watch Webinar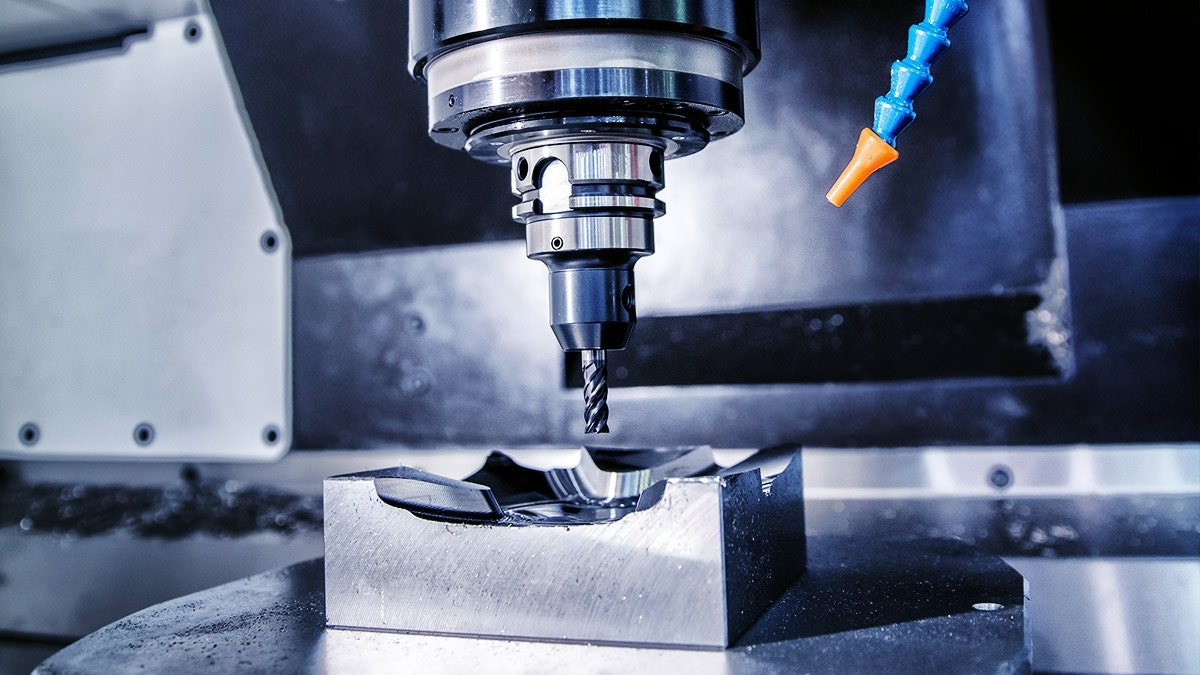
Introduction to SOLIDWORKS CAM
Watch Video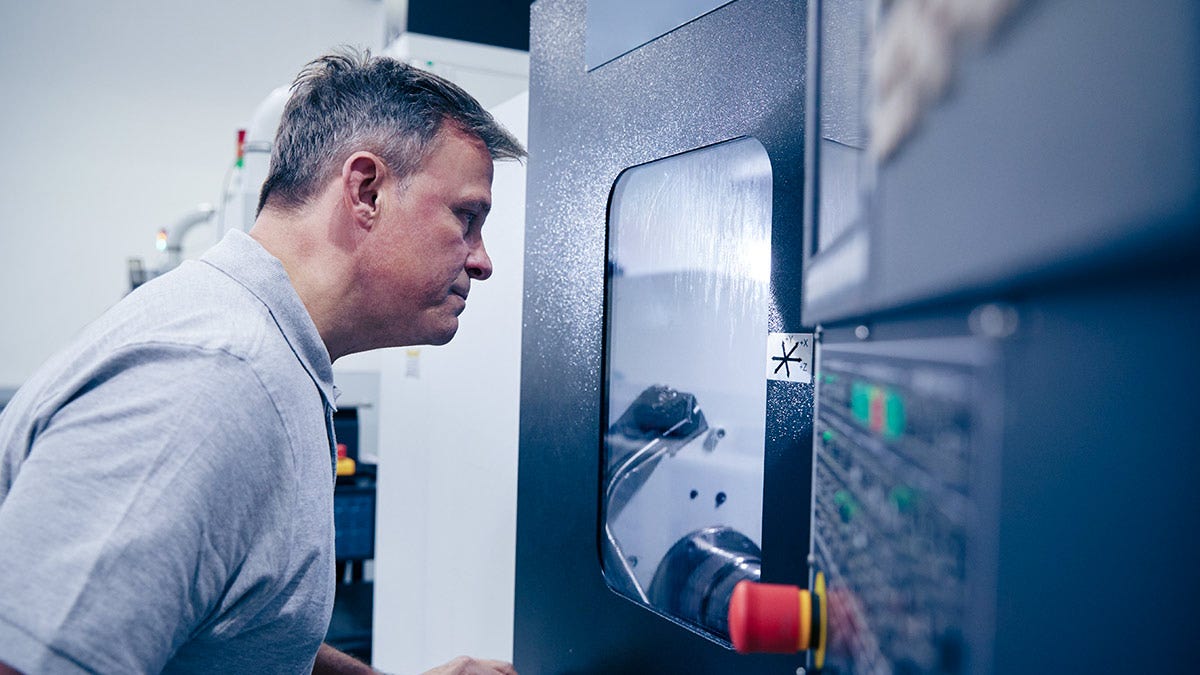
Alien Machine Worx Success With SOLIDWORKS
Watch Video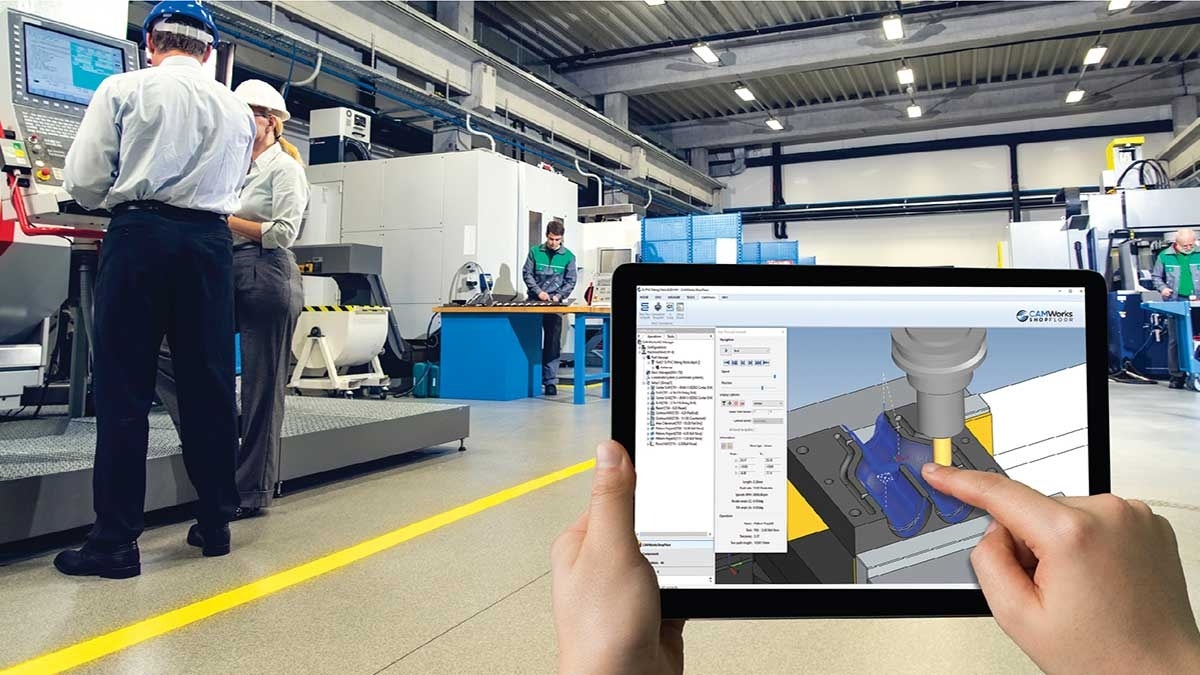
3 Strategies for Reducing Shop Floor Downtime with Industry 4.0 Tech
Read MoreFrequently Asked Questions
One great benefit of our CAM solutions portfolio is the flexibility it offers programmers in selecting the right level for their machining needs. Whether you’re just starting out with entry-level machining using SOLIDWORKS CAM or require more advanced capabilities like 3D to 5-axis machining with CAMWorks, we have the perfect solutions to match your requirements.
No, the hardware requirements are the same as those for SOLIDWORKS.
A post processor is needed, which translates the CAM data into NC code that your machine controller can read. CAMWorks comes with standard post processors, Hawk Ridge Systems has free post processors available for download, and additional post processors can be purchased and supported through Hawk Ridge Systems.
If the file type can be brought into SOLIDWORKS as solid bodies or surfaces, it can be programmed with CAMWorks.
There are three ways to purchase CAMWorks licenses:
- A hardware dongle, which is a USB device that plugs directly into a computer.
- A standalone locked node locked, which is a single software type license that is linked to a client computer’s MAC address.
- A floating network license, which is 1 or more seats of the software that are licensed to the MAC address of a server. The client computers check out the license to use it and return it when they are completed; enabling multiple computers to utilize the license – floating it back and forth.
Yes. CAMWorks is designed to be easy to learn and comes with self-paced tutorials. Hawk Ridge system offers additional training classes, webinars, and blogs for learning resources. We also offer SolidProfessor on-demand training content so you can view training materials whenever and wherever is convenient for you.
Services & Customer Benefits
Technical Support
Our global support team efficiently addresses your needs. We’re here to minimize downtime and costs when your machines encounter issues. If we supply a post processor, expect ongoing support and updates throughout your contract.
Unmatched Training
Our Certified CAM trainers draw from extensive software and real-world machining experience for your productivity. Choose from various training options, including self-paced, instructor-led, and private, tailored to your needs and learning style.
Professional Services
We offer comprehensive CAM and CNC machining software services, including swift implementation, free or customized post processors for seamless software-machine integration, and personalized consulting for ongoing productivity.