Markforged FX20 3D Printer
Get Pricing Sent to You Today
While you are waiting, check out our Resource Center or read our Blog!
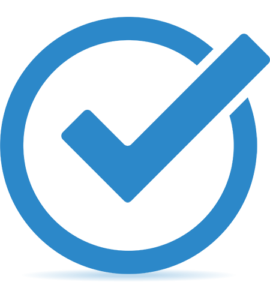
Robust Production of High-Strength, Lightweight 3D Printed Parts
The FX20 brings you a new class of industrial printing systems capable of high-temperature materials – such as Ultem – at larger build volumes and higher accuracies than ever before. Parts you build on this system can withstand high heat, flame, and harsh chemicals found in the most demanding applications. The FX20 also uses the Continuous Fiber Reinforcement (CFR) printing technique unique to Markforged to dramatically increase part strength, providing metal-like strength straight off your machine.
The FX20 is the largest printer available from Markforged. With a print volume 5x larger than any other printer, you can bring the high strength of CFR 3D printing to your largest parts.
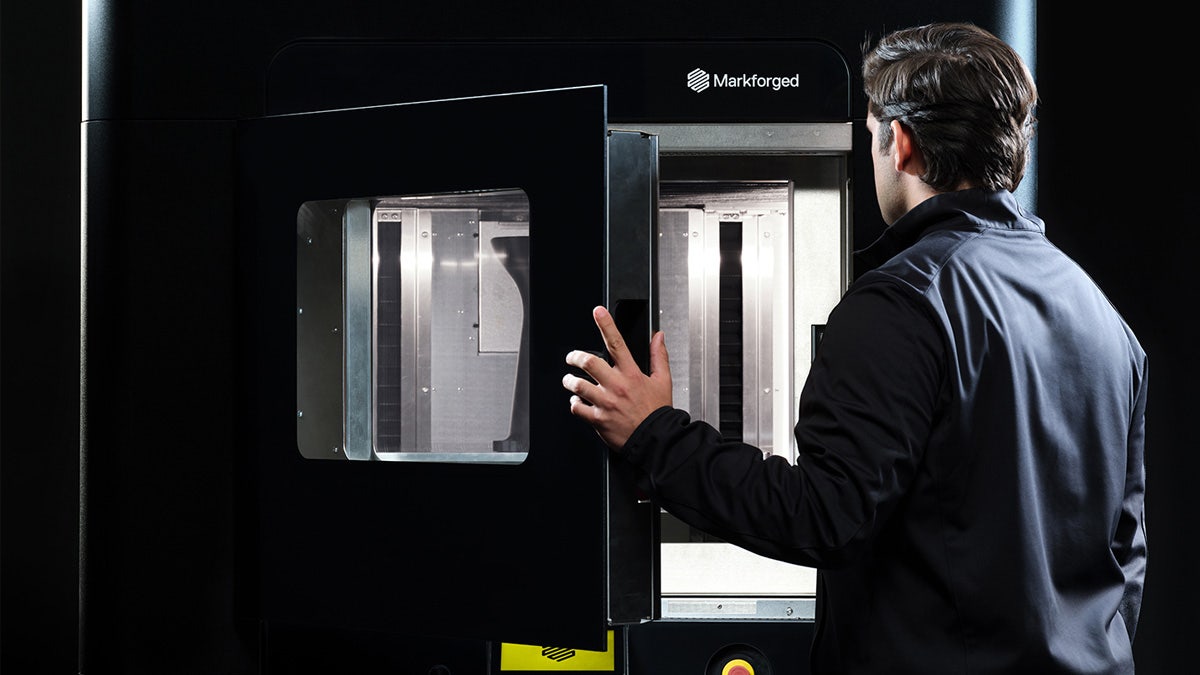
Key Features & Benefits
Large Industrial Print Spools
Heated Build Chamber
Integrated Material Storage
Print Three Materials Simultaneously
Eiger Software
Eiger is cloud-based slicing software for sending and managing print jobs for all Markforged printing systems. The software is free to use; sign up and try it today!
Technical Specifications
Features
|
FX20
|
---|---|
Build Volume
|
Single-Nozzle: 525 x 400 x 400 mm (20.6 x 15.7 x 15.7 in)
Multi-Nozzle: 500 x 400 x 400 mm (19.7 x 15.7 x 15.7 in) |
Layer Thickness
|
125μm minimum, 250μm maximum
|
Machine Size
|
1325 x 900 x 1925 mm (52.2 x 35.5 x 75.75 in)
|
Machine Weight
|
450 kg (1,000 lb)
|
Power Requirements
|
200-240VAC 3P+E, 24A or 347-416VAC 3P+N+E, 14A; 8 kW
|
Elevate Your Manufacturing With the FX20 3D Printer
Unleash the power of advanced additive manufacturing with the Markforged FX20. Engineered for industrial-grade performance, this cutting-edge 3D printer combines precision, reliability, and versatility to revolutionize your production processes.
With the ability to print high-strength parts using a variety of materials, including continuous carbon fiber, Ultem™ 9085, and Carbon Fiber for Ultem™ Filament, the FX20 empowers you to create durable, functional components for a wide range of applications. Take your manufacturing to new heights with the Markforged FX20 3D printer.
Markforged Resources
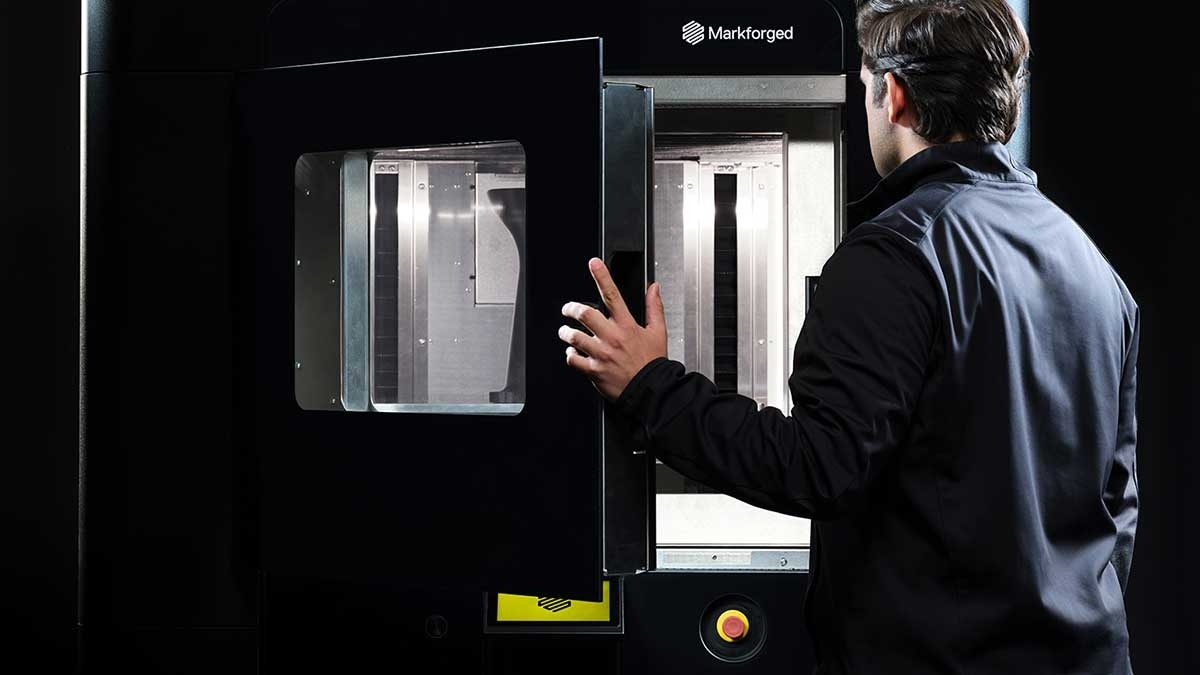
See It Firsthand: The New Markforged FX20
Watch Live Stream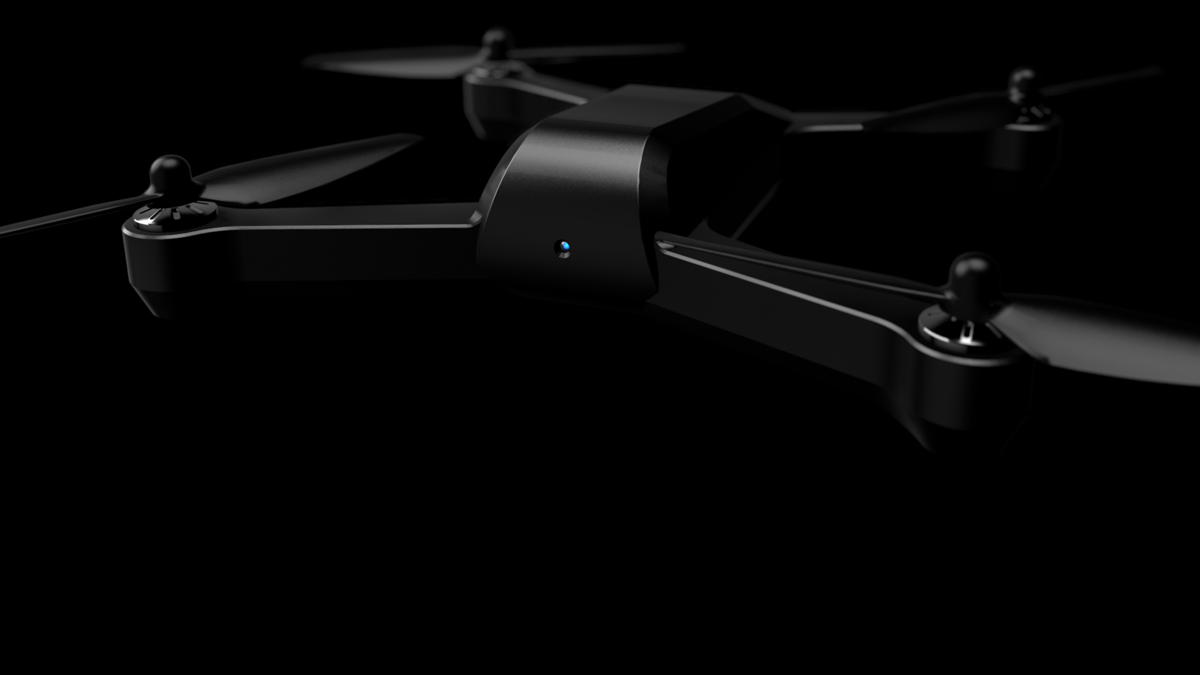
An Overview of Markforged Materials
Watch Video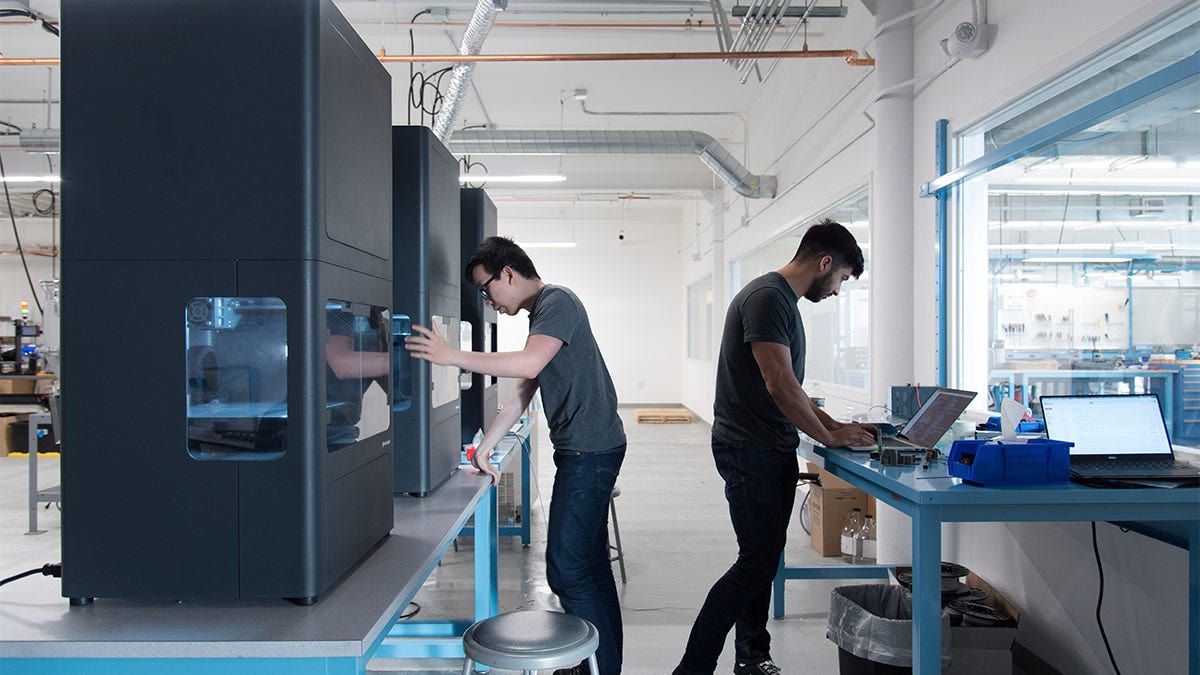
Choosing Your Markforged 3D Printer
Download Guide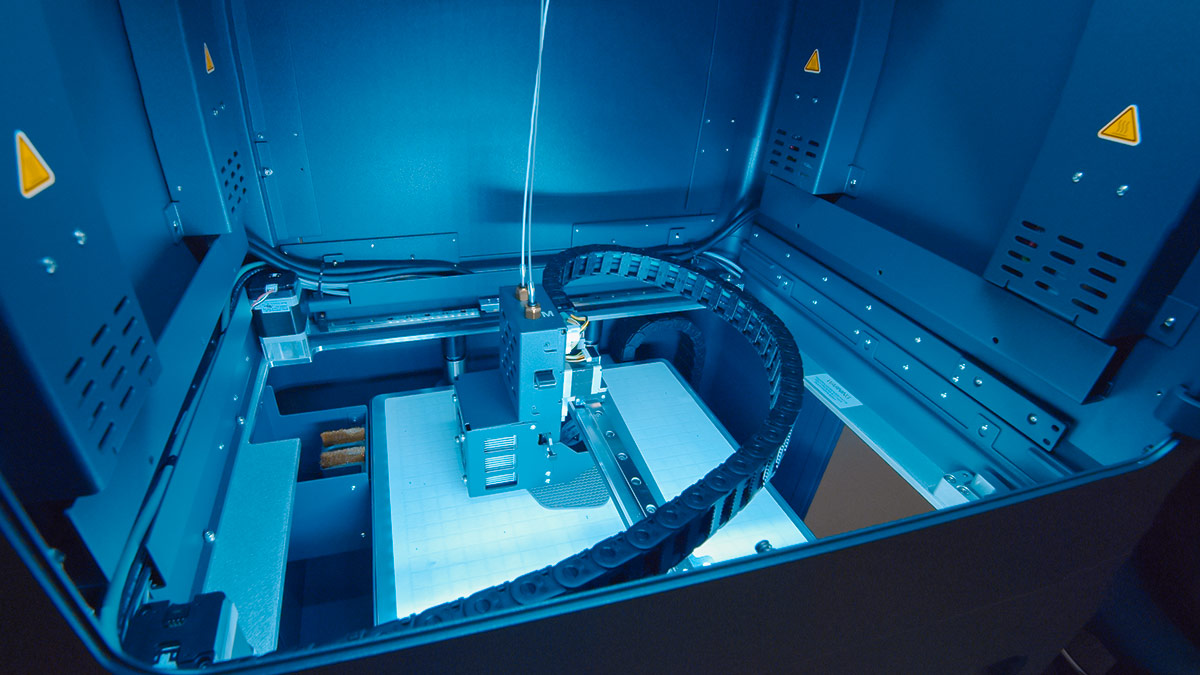
Launching Careers With Markforged
Watch VideoFrequently Asked Questions
The Markforged FX20 offers a generous build volume, allowing users to create large parts or multiple smaller parts in a single print run. The specific dimensions of the build volume can vary depending on the printer’s configuration.
The Markforged FX20 is compatible with Markforged’s Eiger software, a cloud-based slicing and print preparation platform. Eiger offers intuitive tools for importing, arranging, and optimizing models for printing on the FX20, making the printing process seamless and user-friendly.
Yes, the Markforged FX20 specializes in printing parts with exceptional strength and durability. By reinforcing parts with continuous fibers such as carbon fiber or Kevlar during the printing process, the FX20 produces robust components suitable for demanding applications in industries like aerospace, automotive, and manufacturing.
Services & Customer Benefits
Technical Support
Unmatched Training
Hawk Ridge offers complete self-paced training programs for the Markforged line of 3D printers. Learn printer operations, how-tos, and best practices when it’s convenient for you.