CATIA V5
Create, analyze and refine complex designs with high efficiency using robust tools for detailed 3D modeling for large assemblies, simulation and surface design.
Get Pricing Sent to You Today
While you are waiting, check out our Resource Center or read our Blog!
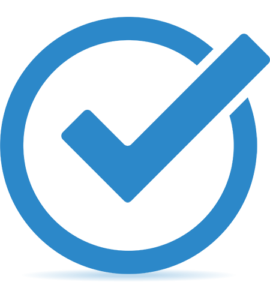
Precision for Complex Engineering
CATIA V5 continues to be the trusted choice for industries requiring high precision engineering and management of complex assemblies.
This robust software suite offers a powerful array of tools for 3D modeling, simulation and surface design, tailored for sectors such as aerospace and automotive where accuracy and detail are paramount. Its proven capabilities support the entire development process from initial concept to final product, ensuring engineers can optimize designs with confidence.
CATIA V5 combines legacy power with sophisticated engineering functionality, making it an indispensable tool in advanced manufacturing.
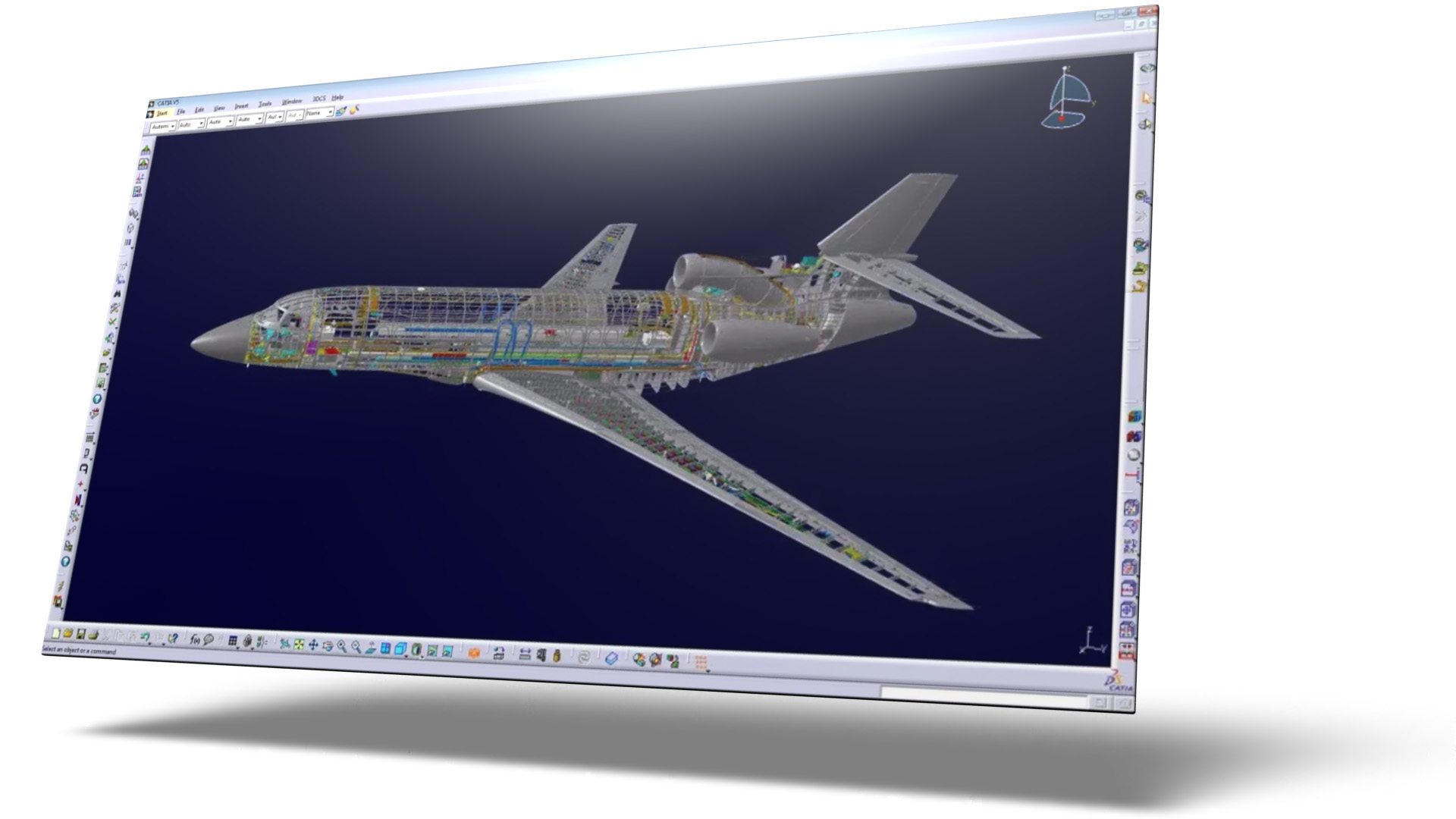
-
Part Design 1
Provides robust tools for creating and modifying 3D solid parts, supporting a range of features, such as extrusions, revolutions and fillets to build complex geometry.
-
Assembly Design 1
Supports the creation and management of complex assemblies by enabling users to position, constrain, and analyze components within a 3D environment, ensuring proper fit and function.
-
Interactive Drafting 1
Enables the creation and modification of 2D drawings directly from 3D models, supporting precise drafting with tools for dimensions, annotations and symbols.
-
Generative Drafting 2
Automatically generates 2D drawings from 3D models, including views, sections and annotations, ensuring consistency and accuracy while saving time in the drafting process.
-
2D Layout for 3D Design 1
Provides tools to create and modify 2D layouts directly linked to 3D designs, enabling synchronized updates and streamlined development of complex assemblies.
-
3D Func. Tolerancing & Annotation 1
Enables the addition of tolerances, dimensions and annotations directly onto 3D models, supporting comprehensive documentation and validation of design intent within the 3D environment.
-
Weld Design 1
Provides specialized tools for defining and managing welds in 3D models, including the creation of weld joints, symbols and annotations, to streamline the design and documentation of welded structures.
-
Sheet Metal Design 2
Offers advanced tools for designing and unfolding sheet metal parts, including features for bends, cutouts and flanges, ensuring manufacturability and efficient development of sheet metal components.
-
Structure Design 1
Facilitates the design and analysis of structural frameworks and supports, offering tools for creating beams, columns and joints to lock in the integrity and stability of structural components.
-
V4 Integration 2
Facilitates seamless interaction with legacy CATIA V4 data, allowing users to import, convert and integrate V4 models, ensuring compatibility and continuity in workflows.
-
IGES & STEP Interface 1
Facilitates the import and export of IGES files, allowing interoperability through the exchange of 3D geometry and design data between CATIA V5 and other CAD systems.
-
CADAM Interface 1
Enables the integration and exchange of data between CATIA V5 and CADAM systems, facilitating the import, export and modification of CADAM drawings within the CATIA V5 environment.
-
Wireframe and Surface 1
Provides tools for creating and editing wireframe geometry and complex surfaces, enabling detailed and flexible design of intricate shapes and features.
-
Real Time Rendering 1
Provides capabilities for real -time visualization of 3D models, allowing users to apply materials, lighting and environmental effects to evaluate design aesthetics and functionality instantly.
-
Tooling Design 1
Provides tools for designing and documenting manufacturing tools and fixtures, including molds, dies and jigs, to support efficient production and deliver high - quality tooling.
-
Object Manager 2
Provides advanced tools for organizing and managing design data, enhancing efficiency in handling complex assemblies through structured storage, retrieval and manipulation of objects.
-
Product Data Filtering 1
Enables the selective filtering and extraction of relevant product data based on specific criteria, streamlining the management and review of complex assemblies.
-
Prod Knowledge Temp. 1
Allows the creation of customizable templates for capturing and reusing design knowledge, standardizing processes and promoting consistency across product development.
-
Knowledge Expert 1
Provides tools for embedding engineering rules and best practices into the design process, automating compliance with standards and enhancing design consistency
-
DMU Engineering Analysis Review 2
Offers tools for evaluating and reviewing digital mock -ups (DMUs) with advanced analysis capabilities, including clash detection, kinematic analysis and simulation, to validate the performance and integrity of engineering designs.
-
DMU Fastening Review 2
Delivers tools for reviewing and validating fastening elements in digital mock -ups, including bolts, screws and welds, ensuring proper placement and assembly in complex designs.
-
DMU Dimensioning & Tolerancing Review 1
Provides tools to review and validate dimensions and tolerances in digital mock - ups, ensuring compliance with design specifications and enhancing the accuracy of virtual prototypes.
-
Part Design 2
Offers advanced tools for creating detailed 3D solid models with features like multi -body design, pattern creation and complex feature editing, supporting intricate part development and robust design workflows.
-
Assembly Design 2
Provides enhanced tools for creating and managing complex assemblies, including advanced constraint management, interference checking and configuration control, ensuring precise fit and functional integration of components.
-
Generative Shape Design 1
Enables the creation and manipulation of complex freeform surfaces and shapes, supporting advanced design capabilities for aerodynamic surfaces, ergonomic forms and intricate geometries.
-
2D Layout for 3D Design 1
Allows the creation of 2D layouts that are directly associated with 3D designs, enabling synchronized updates and facilitating detailed design and documentation of complex assemblies.
-
3D Func. Tolerancing & Annotation 2
Enhances 3D models with comprehensive tolerancing, dimensions and annotations, supporting advanced GD&T ( geometric dimensioning and tolerancing) for precise manufacturing and inspection processes.
-
Functional Molded Parts 1
Provides specialized tools for designing molded parts, including draft, parting line and core/cavity creation, optimizing the design process for manufacturability and ensuring high -quality injection -molded components.
-
DMU Fitting Simulator 2
Enables simulation of the assembly process by checking fit and clearance of components in digital mock -ups, so users can evaluate assembly feasibility and detect potential interferences.
-
DMU Space Analysis 2
Provides tools for analyzing spatial relationships within digital mock -ups, including clearance and interference detection, to ensure optimal component placement and assembly integrity.
-
DMU Kinematics Simulator 2
Simulates the motion of assemblies within digital mock -ups, enabling analysis of mechanisms, detection of collisions and validation of mechanical movements to secure functional performance.
-
Generative Shape Design 2
Offers advanced surface modeling tools for creating highly detailed and complex shapes with precision, supporting iterative design and refinement of intricate freeform surfaces.
-
Generative Shape Optimizer 2
Provides advanced tools for optimizing freeform shapes and complex surfaces to fine-tune designs for performance, manufacturability and aesthetic quality by adjusting surface parameters and achieving smooth transitions
-
Realistic Shape Optimizer 2
Improves shape optimization by integrating real -world constraints and material properties, enabling the refinement of designs to meet performance criteria while ensuring manufacturability and functional realism.
-
FreeStyle Shaper 2
Provides advanced capabilities for sculpting and shaping freeform surfaces, allowing users to intuitively design and refine complex geometries with precision control over surface features and aesthetics
-
FreeStyle Shape Optimizer 2
Provides intuitive tools for refining and optimizing freeform surfaces with real -time feedback, supporting creative exploration and precise adjustment of complex shapes to achieve the desired aesthetics and functionality.
-
Functional Molded Parts 2
Enhances the design of molded parts with advanced features for creating complex parting surfaces, automated core and cavity generation and detailed analysis of moldability, streamlining the production of high -quality molded components.
-
Developed Shapes 1
Supports the creation of flat patterns from 3D curved surfaces, allowing for the development of accurate sheet metal or textile patterns directly from complex 3D geometries.
-
FreeStyle Profiler 2
Offers tools for creating and editing freeform curves and profiles directly on 3D surfaces, enabling the design of intricate contours and the development of complex geometric features with ease.
-
STL Rapid Prototyping 1
Facilitates the export of 3D models in STL format for rapid prototyping, ensuring compatibility with 3D printing technologies and enabling efficient production of physical prototypes from digital designs.
-
FreeStyle Sketch Tracer 1
Enables the tracing and integration of sketches or images into 3D designs, allowing users to overlay 2D sketches onto 3D surfaces to guide the creation of complex shapes and forms.
-
Healing Assistant 1
Provides tools for detecting and repairing geometric imperfections in 3D models, including gaps, overlaps and other inconsistencies, to ensure model integrity and prepare designs for downstream processes.
IMPARARIA SOLUTIONS INC.: Innovating Design and Engineering with CATIA V5
Mansu Kim from IMPARARIA SOLUTIONS INC. uses CATIA V5’s intuitive modeling and centralized data management to integrate client knowledge into advanced models.
With both CATIA V5 and the 3DEXPERIENCE platform working together, the team successfully boosts its accessibility, communication and data sharing across projects.
Services & Customer Benefits
Technical Support
Unmatched Training
We offer complete on-demand training covering everything you need to know to get started with both CATIA V5 and CATIA 3DEXPERIENCE. These are conveniently broken up into easy-to-understand course segments.
Professional Services
We are always here to help and absolutely love a good challenge. From software implementation to design services, if you need anything at all when it comes to CATIA or 3DEXPERIENCE, we are here for you.
Frequently Asked Questions
CATIA V5 is a widely used legacy CAD tool known for its robust 3D modeling and design capabilities across many industries. It typically uses traditional licensing tied to a computer or network server via a license key.
3DEXPERIENCE CATIA builds on V5’s strengths by integrating with the 3DEXPERIENCE platform and using cloud-based named user licensing. This modern approach enhances collaboration, data management and accessibility.
While many companies continue to use CATIA V5 effectively, all current and future development is focused on 3DEXPERIENCE CATIA. Switching to 3DEXPERIENCE CATIA gives you access to the latest innovations and capabilities for modern product development
CATIA V5 is suited for the aerospace, automotive and industrial equipment industries, where managing large assemblies and complex engineering processes is essential. It provides advanced capabilities for surface modeling, system engineering and detailed simulations for these high-demand sectors.
SOLIDWORKS excels in mainstream mechanical design, making it ideal for product development in smaller-scale projects focusing on parametric design and ease of use.
Both tools offer robust design solutions but are optimized for different scales and complexities of engineering tasks.
CATIA V5 offers comprehensive functionality, but the learning curve can vary based on a user’s prior CAD experience. Users familiar with similar CAD tools or earlier versions of CATIA may find the transition smoother.
To support new users, extensive training resources are available, including Hawk Ridge Systems’ SolidProfessor ondemand courses, expert support and consulting services. These resources help users quickly become proficient, allowing them to fully leverage CATIA V5’s powerful design and engineering capabilities.. These resources help users quickly become proficient, allowing them to fully leverage CATIA V5’s powerful design and engineering capabilities.
Yes. CATIA is an excellent choice for managing super large assemblies. It provides advanced tools and performance optimizations, specifically for handling complex and extensive assembly structures. CATIA supports efficient organization, visualization and manipulation of large assemblies, making it ideal for industries like automotive, aerospace and heavy engineering where managing intricate assemblies is crucial
3DEXPERIENCE Resources
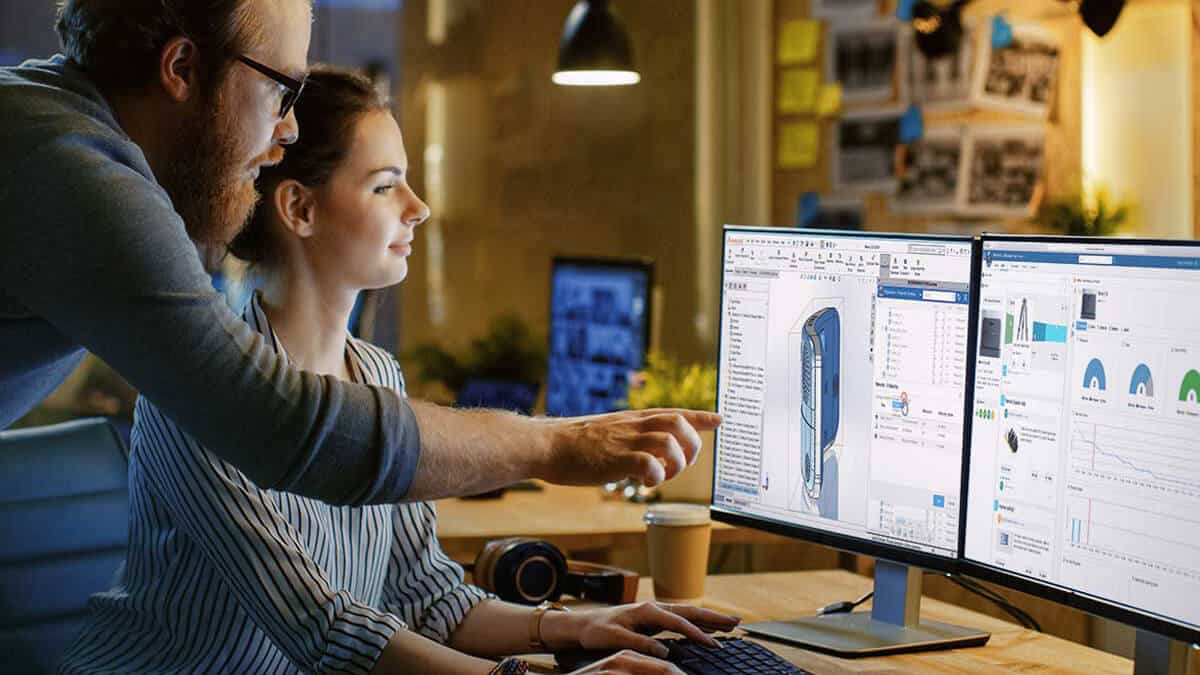
Bring Your Designs (And Your Team) Together
Watch Video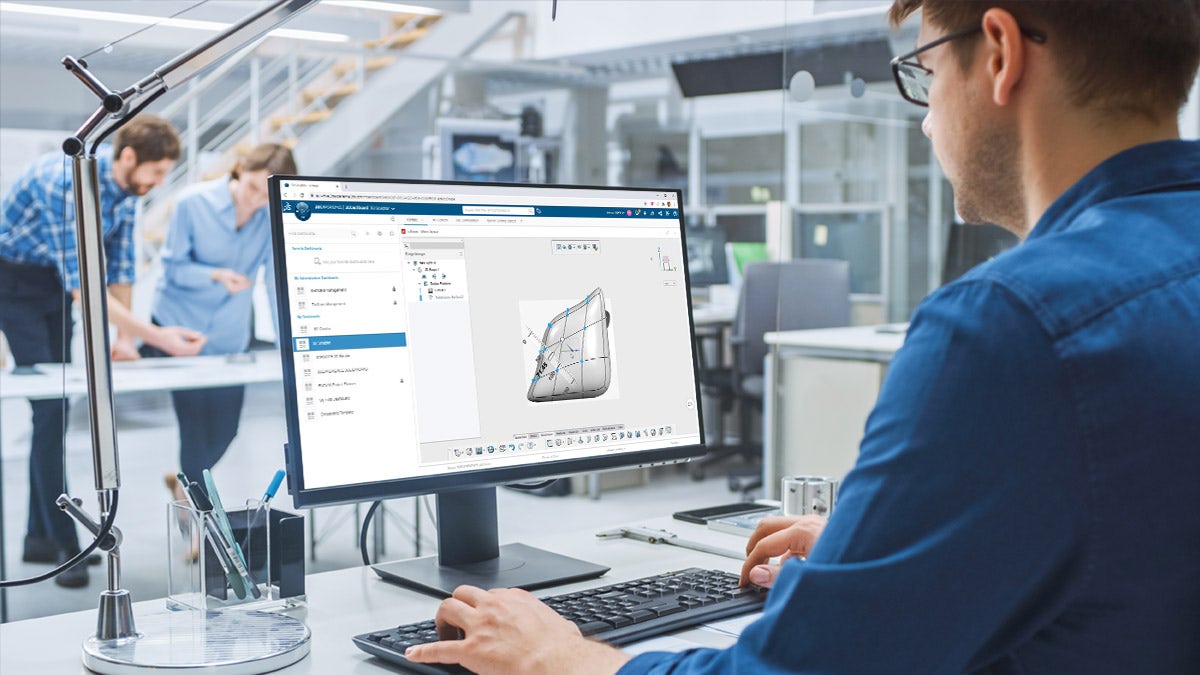
3DEXPERIENCE SOLIDWORKS Overview
Watch Video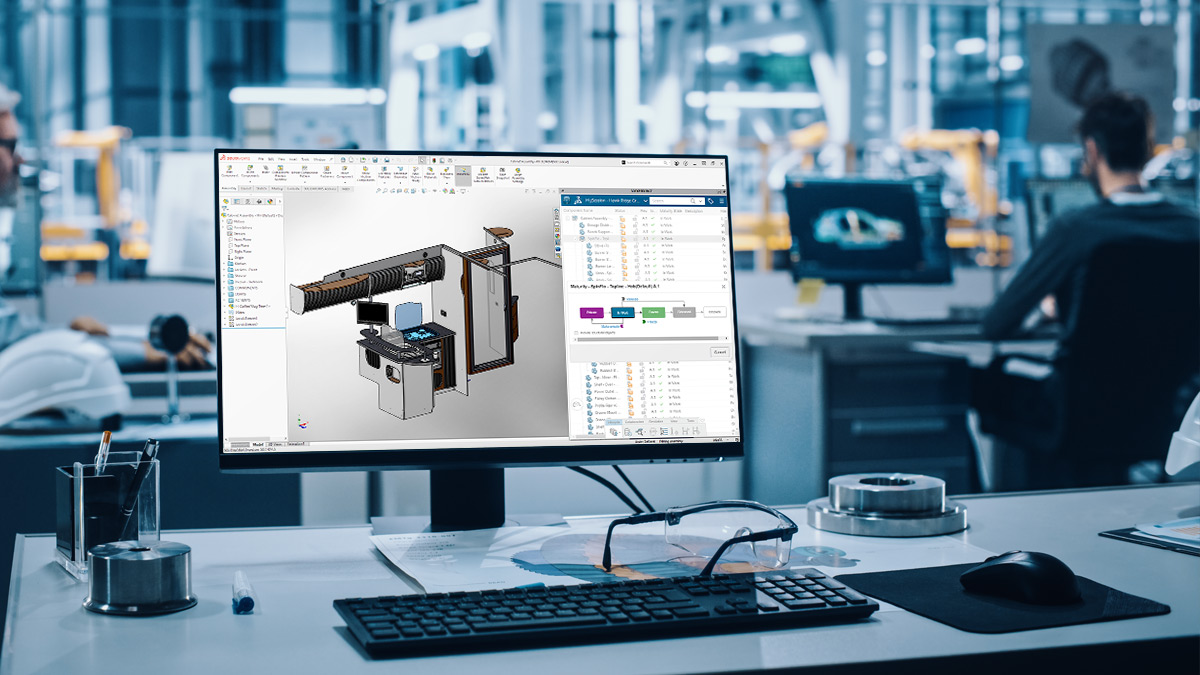
What Is the 3DEXPERIENCE? Let’s Find Out!
Read Article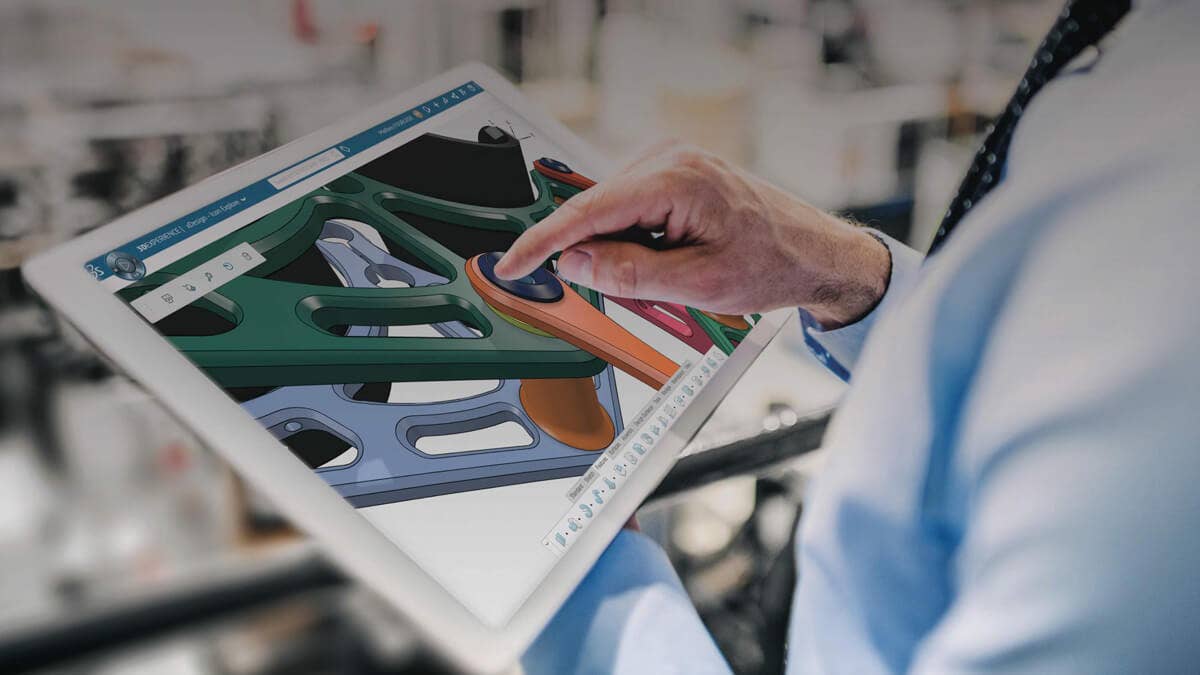