Markforged Industrial Printers
Get Pricing Sent to You Today
While you are waiting, check out our Resource Center or read our Blog!
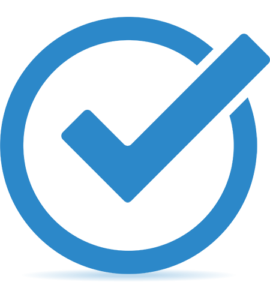
Industrial-Grade 3D Printers Built for Manufacturing
The Markforged Industrial Series of 3D printers are designed to deliver exceptional accuracy, reliability, and repeatability. These large-format printers are built to last, even on the production floor.
Using professional Fused Filament Fabrication (FFF) technology, the Markforged X7 delivers manufacturing-grade parts for end-use applications. These industrial printers are unique in their ability to embed continuous fiber reinforcement into the parts during the printing process to increase strength and stiffness to rival that of metal parts.
Markforged combines robust design, high-precision components, smart technology, and industrial materials to ensure your parts are produced with industry-leading quality at speeds that are impossible with traditional manufacturing methods.
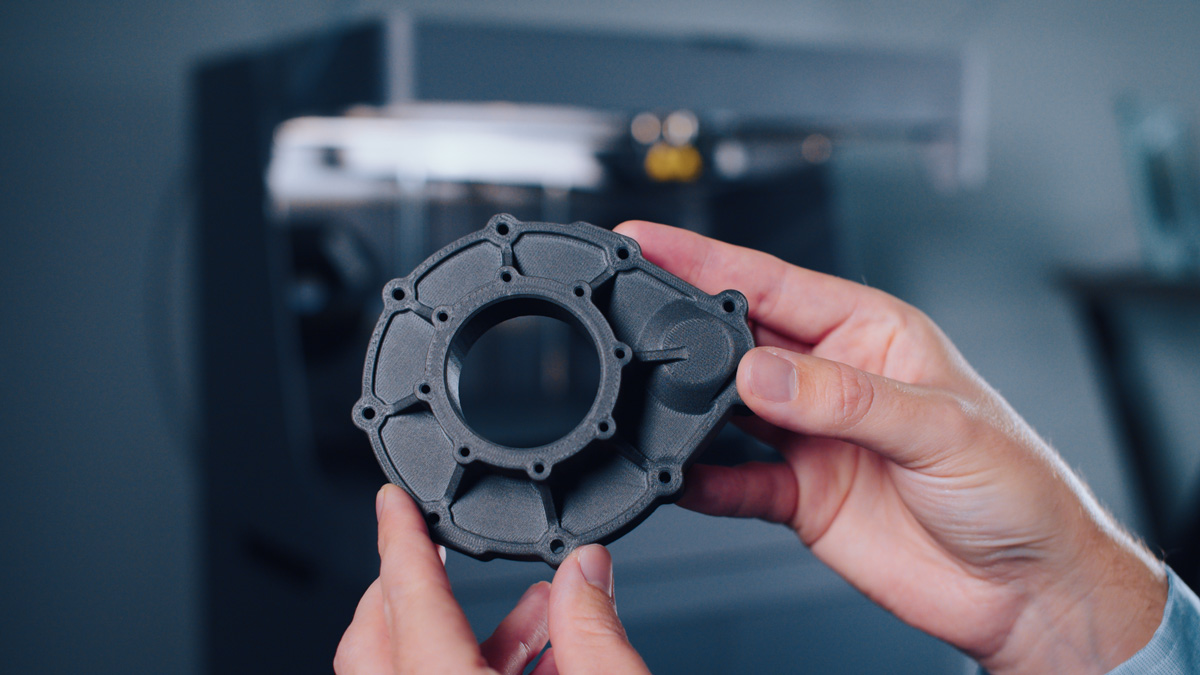
-
OnyxNylon chopped carbon fiber mixed material that is stronger than standard nylon with a black color and excellent surface finish.
-
Onyx FRThis flame-retardant version of Onyx is UL94 V-0 rated (self-extinguishing) and great for applications requiring non-flammable parts. Onyx FR is black in color.
-
Onyx ESDThis electrostatic dissipative material is perfect for protecting electronics. This material is also the strongest plastic that Markforged has to offer. Onyx ESD is black in color.
-
Onyx FR-AOnyx FR-A is a material with lot traceability ideal for aerospace, transportation, and automotive industries. The material is qualified under 14 CFR 25.853 and is currently being qualified in the NCAMP process. Onyx FR-A is black in color.
-
NylonFlexible, soft material with a less abrasive finish, ideal for non-marring work holding applications. Material also can be reinforced with fiber for high-strength applications. Nylon is white in color.
-
FiberglassThe most affordable fiber that will reinforce your parts and still achieve significant rigidity improvements.
-
HSHT FiberglassA very strong fiber that has the highest heat deflection temperature of any Markforged fiber, HSHT Fiberglass is perfect for high-temperature applications.
-
Carbon FiberCreate parts stronger than aluminum utilizing the highest tensile strength fiber that Markforged has to offer.
-
Carbon Fiber FR-ACreate parts stronger than aluminum utilizing the highest tensile strength fiber that Markforged has to offer.
-
KevlarImpact-resistant fiber with higher elongation to break, perfect for applications with sudden high loads.
-
Continuous Fiber Reinforcement (CFR)Create parts with aluminum-like strength by reinforcing plastic parts with continuous fibers.
-
Eiger SoftwareCloud-based slicing software for sending and managing print jobs for all Markforged printing systems. The software is free to use; sign up and try it today!
-
Turbo PrintExtreme print speed functionality with 250 micron layer heights, ideal for larger geometries.
-
Inspection Software
Inspection features in-process laser inspection capabilities, allowing automated scanning of parts as they are being printed using an on-board laser micrometer.
-
Offline EigerThis offline, subscription-based version of Eiger software is designed for companies that require higher security measures.
Technical Specifications
Features
|
Markforged X7
|
---|---|
Build volume
|
13” x 10.63” x 7.87" (X,Y,Z) 330mm x 270mm x 200mm
|
Layer thicknesses
|
50 micron, 100 micron, 125 micron, 200 micron, 250 micron (Turbo Print)
|
Model base materials available
|
Onyx, Onyx FR, Onyx FR-A, Onyx ESD, Nylon
|
Reinforcement fiber materials available
|
Fiberglass, HSHT Fiberglass, Carbon Fiber, Carbon Fiber FR-A, Kevlar
|
Overall size of machine
|
23” x 19” x 36" (X,Y,Z) 584mm x 483mm x 914mm
|
Weight of the machine
|
106 lbs / 48 kg
|
Power requirements
|
100-240VAC, 150W (2A peak)
|
Revolutionizing Dragsters With Markforged
In the high-speed, high-stakes world of jet engine drag racing, manufacturing quality parts is a matter of life and death. Just ask Josette Roach, one of only five female jet dragster drivers in the entire world.
Josette Roach and Brian Tocci of Larsen Motorsports saw the need to create a custom steering wheel for Josette’s jet car that would fit her hands exactly. Enter Markforged, and our Simulation software, which allowed the team at Larsen to build this part with top-end accuracy.
Markforged Resources
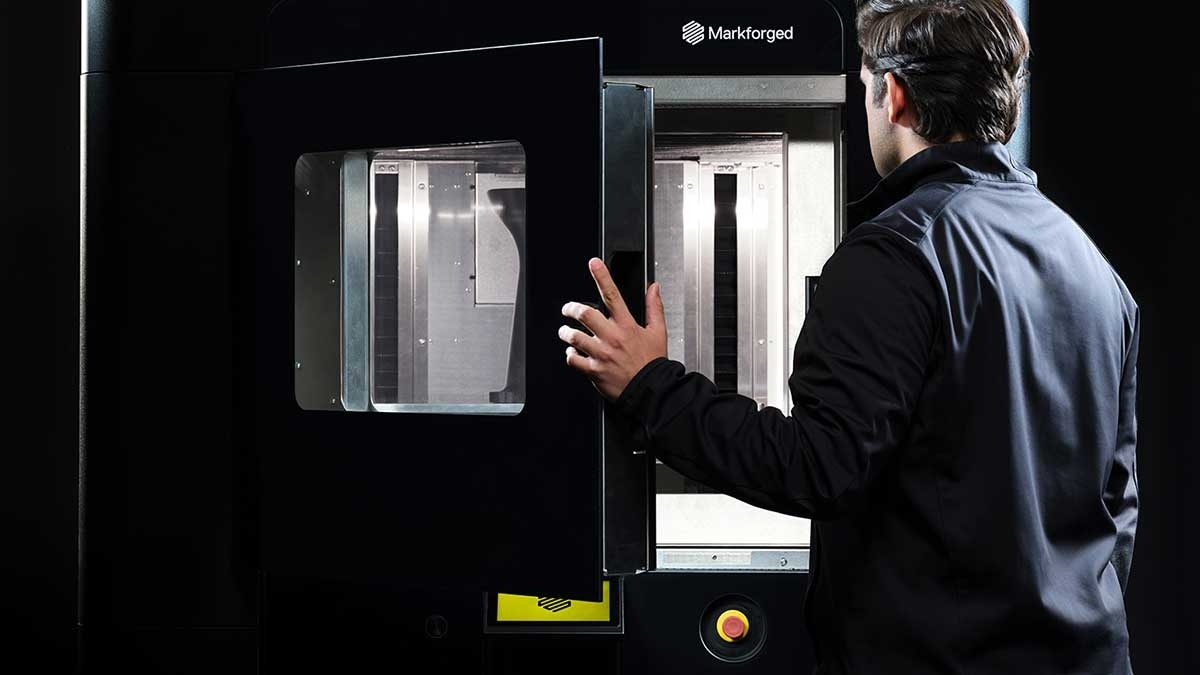
See It Firsthand: The New Markforged FX20
Watch Live Stream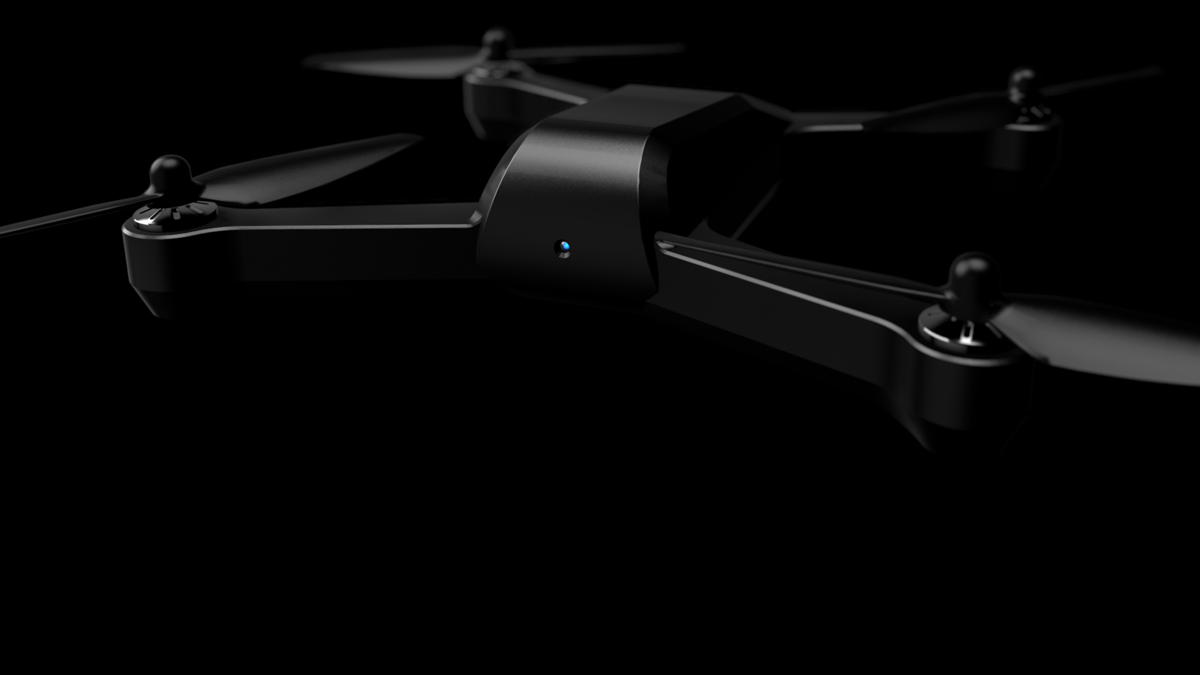
An Overview of Markforged Materials
Watch Video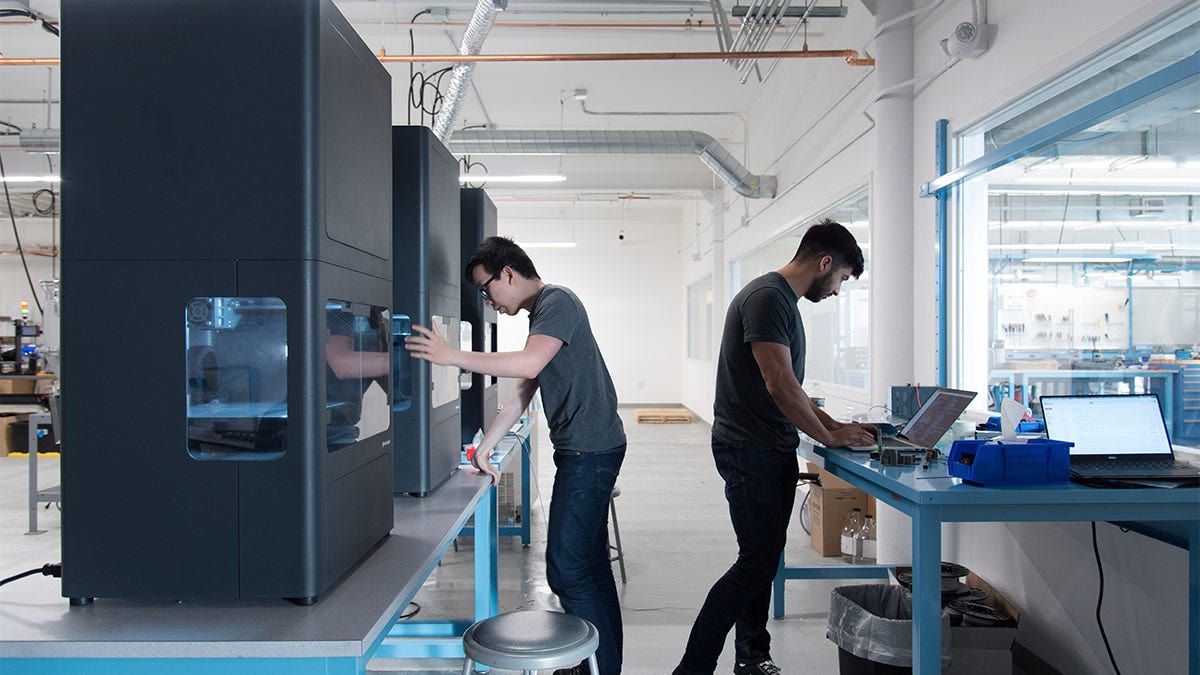
Choosing Your Markforged 3D Printer
Download Guide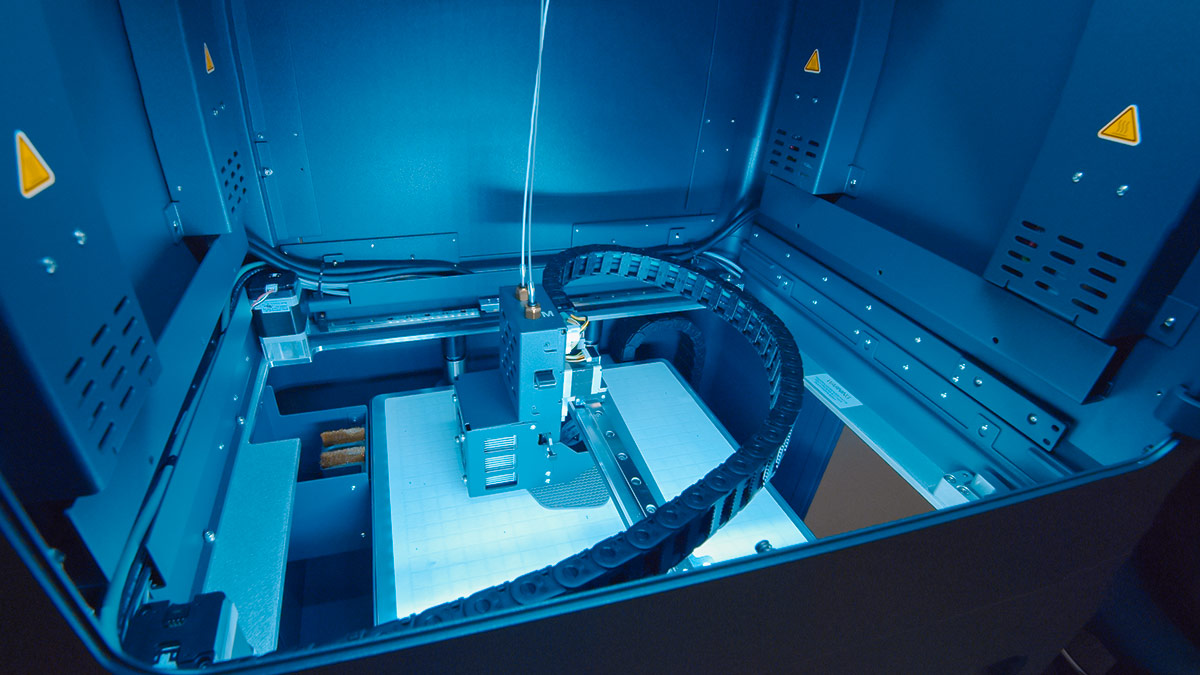
Launching Careers With Markforged
Watch VideoFrequently Asked Questions
Services & Customer Benefits
Technical Support
Unmatched Training
Hawk Ridge offers complete self-paced training programs for the Markforged line of 3D printers. Learn printer operations, how-tos, and best practices when it’s convenient for you.